APM WINMACHINE FEATURES
ELEMENTS - APM Bear - APM Plain - APM Joint - APM Spring
APM Bear is a state of the art software for the calculation of non-ideal bearing parameters.
APM Bear Rolling contactbearings are the main type of supporting units for rotating parts of machines,instruments, apparatuses, various mechanical devices and systems. APM Bearperforms a complex analysis of rolling contact bearings. When using it you cancalculate main bearing characteristics and select the optimal constructions ofthe bearing units. Highly effectivemethod of the non-ideal bearings calculation.
APM Bear is a state of the art software for the calculation of non-ideal bearing parameters.
A bearing is considered non-ideal if its manufacturing errors cannot be ignored in the context of the problem to be solved. Many important problems of thecontact stiffness and strength require a bearing to be considered non-ideal.The Centre APM has developed the universal method for solving contact problems.Reliability and effectiveness of this method are proved by series of the experimental researches. The most important bearings parameters are calculated. Our software helps to design rolling-contact bearing optimum by stiffness and other criteria.
Types of bearings
Radial BallBearing - Self aligning BallBearing - Radial-Thrust BallBearing
Thrust BallBearing - Radial RollerBearing - Self aligningRoller Bearing
Radial-ThrustRoller Bearing - Thrust RollerBearing.
Any Special Type Of The Bearing You Need Bearing behaviour modelling instead of the single parameter’s calculation
When speaking about modelling we mean that with the APM Bear you are not restricted to the determination of the averaged (or the most probable) parameters values, but rather you are given a possibility to model the behaviour of your bearing. To give you such a possibility a reasonably large series of the parameters valuesare calculated. They show how these parameters are changing. By using thesedata you can determine the features of distribution, maximum deviations, fieldsof dispersion, etc. Together with the macro characteristics you are given a look into microcosm of your bearing.
Main features -APM Bear
Displacements (Stiffness) - Maximum ContactStress
Forces Acting OnThe Rolling Bodies - Longevity- Loss Of Power
Moment Of Friction - Heat Release - Initial dataentering
User interface is straight forward and intuitively clear. In order to learn how to work with the APM Bear you need no more than1—2 sessions. You can enter all geometry data manually or select from mechanical database that is a part of APM WinMachine system. Accuracy parameters can be selected from the database according to accuracy class byrequest. You can set variable external loads by means of corresponding graphical editor. Calculations in the APM Bear can be made for any combination of axial and radial forces, the axial and radial preload allowed for the bearing of thegiven type
Displacements andstiffness — a keystone in the bearing calculation
Determination of the displacements and stiffness is the key stone and at the same time thes tumbling-block of the bearing parameters calculation..
Forces acting onthe rolling bodies During the rotation of the bearing its rolling bodies are subject to the normal forces actions applied from the raceways and depending on the geometry, accuracy, external load, etc.
Existing methods over idealize the problem that produces over simplifiedsolution. A new approach was developed. It gives a more real picture. The forces acting on the rolling bodies are calculated in the APM Bear for the each member of the large series of the bearing center positions determinedduring the bearing displacements calculation. As a result you are given apossibility to trace how these forces change in time.
Safety parameters — longevity and maximum contactstress
The maximum contact stress calculated in the APMBear is the stress in the contact of the most loaded rolling body. You can test whether it satisfies the required strength condition.
The longevity is the time period during which 90 of each 100 bearings will not have a fatigue failure.
Energetical parameters — friction in the bearing
Accuracy Class Is An Important Parameter Characterizing Bearing Work And Is Directly Connected With Shaft Displacements. These Displacements Can Have In General Case Axial, Radial And Sided Components Depending On Bearing Type.
For Statistical Dispersion Analysis Of Output Bearing Parameters TheirCalculation Is Performed In 100 Arbitrary Positions Of Bearing Center. The ResultsOf Loads Calculation Let To Define Energy Characteristics: Efficiency, Loss OfPower By Friction, Heat Release, Etc.
With The Help Of APMBear You Can Determine Three Parameters Characterizing The Action Of TheFrictional Forces:
Moment OfFriction - Loss Of Power - Heat Release.
Distribution Of Rolling Bodies Loads Makes A Significant Influence On Bearing Longivity. Longivity Calculation Comes To Determination Of Bearing Working Time Till Spalling Start Of Race.
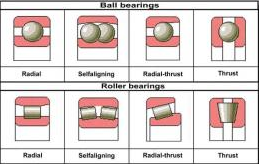
Types of bearings
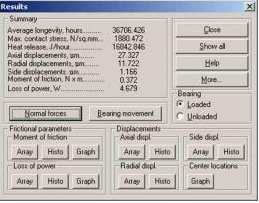
Dialog box Results
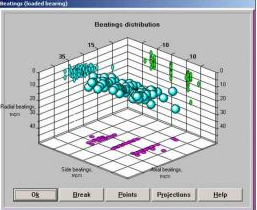
Bearing 3D distribution
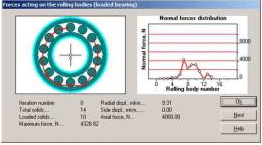
Forces on rolling bodies
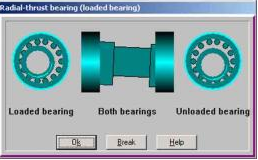
Animation
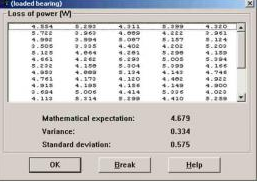
Axial runout histogram
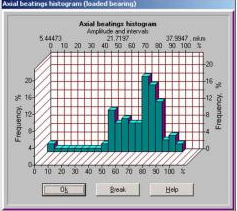
Loss of power table
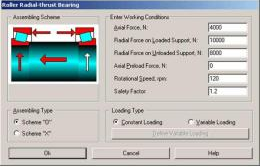
Entering working conditions
Result representation
Tables Of Static Characteristics - Histograms Graphs Of Parameters Depending On Rotation Angle 3D Field Of Bearing Center Position
Animation Of Bearing Movement All This Forms Of Presentation Give Authentic View About Bearing’s Movement. You Can Turn The Frictionless Bearing In Order To Watch Changing Applied Bearing Loads.
APM Plain
APM Plain Plain bearing is an important type of the rotation supports that is frequently used in complex environments under high vibration and shocks,very low and very high rotational speed, high demands on the shaft stability and accuracy, for the units working in the water and in the aggressive environments, in the absence or lack of the lubrication, etc.
The reliability of the bearings determines the reliability of the equipment they are installed in. APM Plain performs a complex analysis of the plain bearings. When using the system you can determine the basic parameters of the bearing and select the optimum construction of the bearing unit.
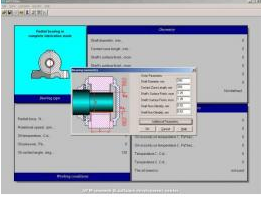
INITIAL DATA
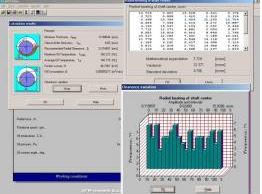
Calculation results
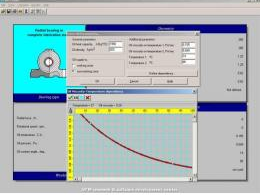
Oil parameters
Plain bearingtypes - Radial Bearings - In Fluid Lubrication Mode
Radial Bearings - In Semifluid Lubrication Mode
Thrust Bearings - In Fluid Lubrication Mode
APM Plain One Can Calculate Radial And Axial Clearance Distribution -Optimum ClearanceValue Lubrication SystemParameters (Oil Film Thickness - Maximum And Average Oil Temperature - Oil Consumption) -True Friction Coefficient And Loss Of Power - Optimum Dimensions Of The Bearing Elements. Calculation criteria and methods - Calculation criterion for radial bearings that work in the fluid lubrication mode is the condition of minimum allowed clearance between bearing contact surfaces
Calculation criterion for radial bearings that work in the semifluid lubrication mode isrequirement for bearing working temperature to be less than the maximum allowedone for given oil.
Calculation of radial bearings that work in the fluid lubrication mode is performed by Reynold's equation solution. So the fluid flow is considered to be laminar.
Calculation methodof radial bearings that work in the semifluid lubrication mode is based onanalysis of heat release by friction and solution heat transfer equations.
Download APM Plain Demo
APM Joint - APM Joint is a software for the machine element joints calculation and design.It allows to perform a complex calculation and analysis of the most widely used types of joints. The use of this software reduces design time, increases design reliability and efficiency, helps to select the optimal decision.
APM Joint - Elements and units of the machines, mechanisms and constructions are joined together by means of the special elements or without them, producing new constructions and units as the totality of the smaller ones. There are many ways of element joining and many methods of the calculation and the design of such joints. Different types of machine element joints are used in the mechanical engineering— threaded,welded, riveted, keyed, splined, etc. You can design and calculate all these objects with the APM Joint. APM Joint is a software for the machine element joints calculation and design. It allows toper form a complex calculation and analysis of the most widely used types of joints. The use of this software reduces design time, increases design reliability and efficiency, helps to select the optimal decision.
APM Joint can calculate the following joints
Threaded openedand closed joints , with any elementarrangement, arbitrary configuration of surfaces to be joined and arbitraryloading In addition bolts, screws and studs can be calculated as fasteningelements under arbitrary external load
Welded joints with the arbitrary arrangement of seams underthe arbitrary external load, including butt joints - tee joint - lap joints jointsproduced by the spot weld. rivetted joints ofthe arbitrary arrangement under the arbitrary plane loading
Joints of therotating elements such as - interference fitsof the cylinder and cone shape - splined and keyedjoints - radial and axialpins (gluts)
joints with conerings - terminal joints - profile joints
APM Joint calculations
The criteria for the threaded joints calculation is the absence of the shearing and the absence of the opening of the conjagate surfaces, as well as the static strength and the fatigue strength; welded seams are calculated for the static and the fatigue strength; rivetted joints are checked for the strength under the constant load.
APM Joint calculations
Either absence of the shearing and non-opening or the static and the fatiguestrength of the joint elements or both the former and the latter can be used(depending on the type of the joint) as a criteria for the joints of therotating elements.
It is possible to create the designed models bothin APM Joint editor and in other graphics systems, which support export to*.dxf.
Besidescalculation facilities APM Joint provides user with the functionally completeintegrated environment that includes:
specializedgraphical editor
versatile toolsfor calculation results presentation
editable built-indata base - dxt files importfunctionality
Completeintegrated environment
APM Joint allowsto perform all types of the design and checking calculations. The formerincludes determination of the joint dimensions for the given loading, the latter— the safety factors calculation.
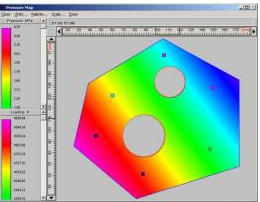
FEM ANALYSIS
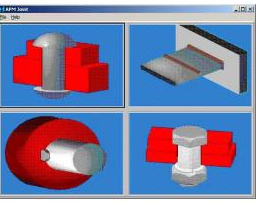
Selectiontype of Joints
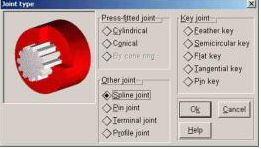
Selection type for the rotating joints
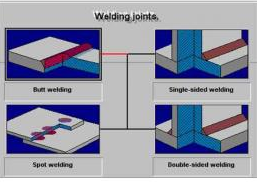
SelectionType of Welded Joints
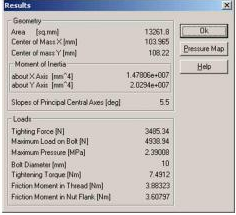
Calculation results
APM Spring - APM Spring Machine elements that have high compliance and minimum dimensions are called elastic elements.They are used as loading devices, as shock absorbers, dissipating energy of the shocks, as devices for the energy accumulation, etc. Elastic elements are of significant importance for the modern machines by increasing longevity of the latter due to the vibration damping and to the resonance...
APM Spring
Machine elements that have high compliance and minimum dimensions are called elastic elements.They are used as loading devices, as shock absorbers, dissipating energy of the shocks, as devices for the energy accumulation, etc. Elastic elements are of significant importance for the modern machines by increasing longevity of the latter due to the vibration damping and to the resonance frequencies regulation.
Features - Various springs design - Static and fatigue calculation - Working drawings generation - Adding new materials and correction of the existent.
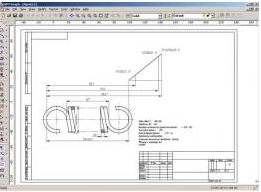
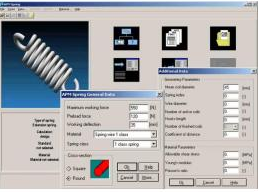
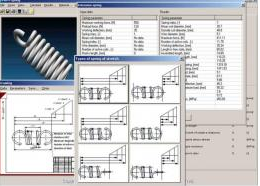
APM Spring is a system for the calculation and design of elastic machine elements. It allows toperform design and checking calculations and to generate working drawings ofelastic elements. Design calculations allow to determine dimensions of elasticelements based on the given external loading and on deformations. Checking calculations allow obtaining strength safety factors depending on the elastic element dimensions.
Types of elasticelements
Cylindrical tensional springs with round and rectangular cross-section - Cylindrical compression springs with round and rectangular cross-section
Cylindrical torsion springs with round and rectangular cross-section - Disk compression springs - Flat rectangular springs - Torsion bars.
Types of elastic elements
Calculations can be made for both constant and variable loading. The calculations are based on the determination of the static strength under constant loading and of the fatigue strength under variable loading. It is possible to perform the finite element analysis of a spring in APM Structure 3D module. Working drawings generation - APM Spring allows generating complete working drawing of the springs and torsion bars. Drawing is created in APM Graph file format and can be exported in DXF format using APM Graph functionality.
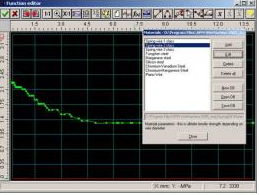