MECHANISM IN AUTOMOBILE
General
Summary keywords
- planar mechanisms
- design and simulation
- CAD interface, dxf import
- synthesis
- video export
- documentation
- 5 languages
- support by engineers
SAM can also animate the mechanism motion.. As a further aid for the designer the path and velocity hodograph of any number of moving points can be plotted. Also, a complete project documentation (ASCII-format) can be automatically generated.
CAD interface
The DXF import/export facility lets you export your conceptual mechanism design to any CAD program to work out the details and it lets you import CAD data to easily set-up the mechanism in SAM or to perform animation of the final mechanism.
Optimization: Driving torque minimization, Path Optimization
Display: Animation/path/hodograph/colors
SAM (Synthesis and Analysis of Mechanisms) is an interactive PC-software package for the design, analysis (motion and force) and optimization of arbitrary planar mechanisms. Mechanisms can either be generated via the design wizards or they can be assembled from basic components including beams, sliders, gears, belts, springs, dampers and friction elements. SAM integrates pre-processing, numerical analysis and post processing, such as animation and xy-plots, in an easy to-use environment offering pull-down menus, mouse support and help facilities.
The mathematical foundation of the analysis kernel, which is inspired by the well-known finite element approach, offers a large number of features and overcomes many of the problems of traditional mechanism programs. Open loop, closed loop, multiple loop and even complex planetary mechanisms can equally well be analyzed due to the finite element formulation. Even the most complex mechanisms, including planetary gear trains, can be modeled within minutes
SAM is available in English, German, Spanish, French, Dutch and Chinese.
Post-processing
The analysis results can be displayed either in tabular or graphical form. The tabular listing can be viewed on the screen, send to a printer or stored in a readable formatted list file. The x/y plot option allows to plot any variable against time or any other variable. An unlimited number of functions can be combined into one x/y plot with optionally two different scalings to allow proper multiple display of variables with different amplitude ranges. It is possible to output selected data to an external file (ASCII format) for customized post-processing.
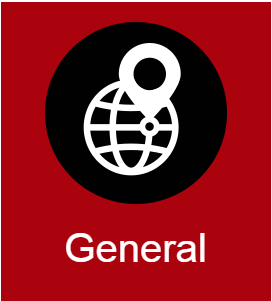
Video tutorials
Build:
Beam , Slider, Belt, Gear, Spring, Sensor, Import/export a mechanism
Graphics:
Create/edit/attach, Import, Export
Input Motion:
Targets: Angle/elongation, Relative angle, X/y position, Various ways of driving a mechanism
Modelling
SAM is equipped with a large library of basic elements, including:
- beam, slider
- belt, gear
- sensor
- spring, damper and friction element (both translational and rotational)
- non-linear spring
which allows the analysis of a huge variety of mechanisms. The unique mathematical foundation of the program offers a large number of features and overcomes many of the problems of traditional mechanism programs. Open loop, closed loop and even multiple loop mechanisms are treated in the same way and even the most complex mechanisms, including planetary gear trains, can be modeled within minutes.
CAD interface
The DXF import/export facility lets you export your conceptual mechanism design to any CAD program to work out the details and it lets you import CAD data to easily set-up the mechanism in SAM or to perform animation of the final mechanism. Imported CAD parts may be used as illustrative parts of the mechanism.
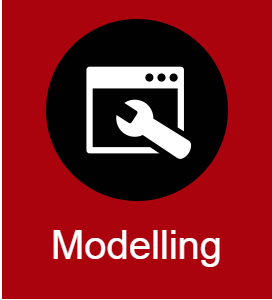
Analysis Results
Keywords
- positions, angles, length
- derivatives
- force and torque
- power
- bearing forces
- path, hodograph
- user expressions
- export
Once the mechanism has been constructed and the inputs have been defined any of the following kinematic quantities can be calculated (all relative or absolute):
- nodal position, displacement, velocity, acceleration
- angles, angular velocity and acceleration
Furthermore SAM can perform force-analysis, thus enabling the calculation of:
- driving torque (force)
- reaction forces in bearings
- internal forces in elements
- required or transmitted power
User defined results (SAM Professional)
A sophisticated formula parser offers the possibility to combine simulation results in multiple ways to
derive user defined results. User defined results may also be displayed as curves in the graph.
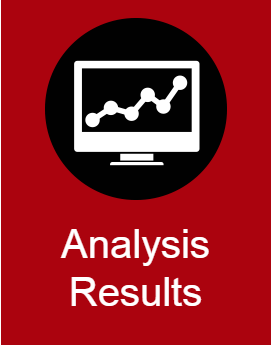
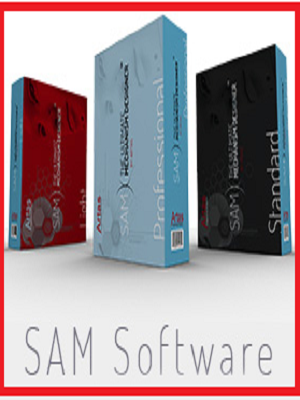
Input Motion
Keywords
- user table
- multiple actuators
- linear actuator
SAM allows the definition of multiple inputs, which can either be defined in terms of absolute displacements or in terms of elemental change of shape to model relative inputs (e.g. elongation of a hydraulic cylinder or relative rotation of a robot elbow). Each of the inputs can be defined independently. Various frequently used input motion laws, such as:
- constant velocity
- polynomial
- cyclical motion
- 2.order velocity profile
- cubic splines
are available and can be combined to form any desired input diagram. Inputs can also be read from an external ASCII file or defined via a table to enable the definition of arbitrary motions. This latter feature is especially handy for the modeling of non-standard cam profiles.
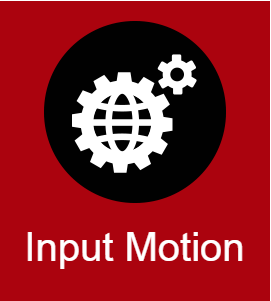
Optimization
Keywords
- all geometry
- single function
- multi parameter
- constrained optimization
- function or path
- mass, stiffness
- position of mass
- peak, RMS, average
The optimization module of SAM Professional offers constrained single-function multi-parameter optimization based on a mix of evolutionary algorithms and Simplex techniques. Constraints are dealt with by treating each
violation of a constraint as a penalty that is added to the original cost function. The software offers the
option to define own results from the standard set of results via an advanced formula parser. This option
is also used to define and add penalties.
Taking the initial design/topology as a starting point one can for example further improve the quality in
which the trajectory of a coupler point equals the target trajectory by changing the geometry of the
mechanism within pre-defined ranges. Or one can minimize the peak or RMS value of the driving torque
of a mechanism by adding a compensating mass and let SAM determine the optimal value of the mass
and its position within the allowable range. Just as in the case of the trajectory optimization one can
also specify a reference function and minimize the difference between the actual and the reference
function. When designing for example fitness equipment one is generally seeking a predefined force as
function of displacement.
The goal for optimization can be the minimization or maximization of a variety of properties (peak, RMS, average, ...) or the difference between the actual and the target behaviour of a mechanism, such as:
- Trajectory of a node (with of without prescribed timing)
- Any motion or force quantity (as function of time or another quantity)
SAM seeks the optimum by modifying the following properties within user-defined ranges:
- geometry of mechanism
- element properties, such mass, spring constant, transmission ratio, ...
The optimization process in SAM is based on a two step approach, consisting of:
- Exploration of the design space
- Optimization of a specific solution
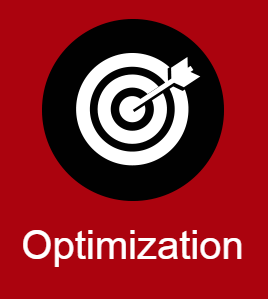
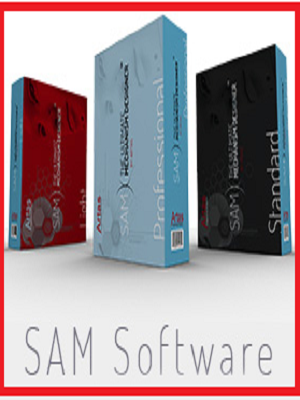
First, the entire parameter space is explored globally using a combination of a pure Monte-Carlo technique and a so-called Evolutionary Algorithm, which is a optimization technique derived from Genetic Optimization. The top list of such a global exploration are shown in the Explore list box, which displays the value of the optimization function and the corresponding parameters. The individual with the best property is listed at the top.
Next, the designer can select one of the results from the Explore window and start a local optimization. This local search can be either based on a Simplex technique or on a Evolutionary Algorithm with a smaller parameter range centered around the selected solution.
The combination of a global exploration strategy and a local optimization strategy - with the designer in the loop for selecting the mechanism that is further optimized - is believed to give the best trade-off between speed and coverage of the design space. Alternatively, options can also be set in such a way, that a fully automated optimization is performed.
Design Wizards
Keywords
- parametric
- 4-bar mechanisms
- exact linear guiding
- approximate linear guiding
- Watt, Evans
- Robberts
- Chebyshev
- Hoecken
SAM offers a set of design wizards which will help you to synthesize mechanisms for specific tasks, such as:
- Angle function generation (a minimum of 3 pairs of input/output angles are to be satisfied).
- 3-Position/angle synthesis of the coupler plane
- Approximated straight line motion
- Exact straigh line motion
In case these design wizards do not provide the solution to the specific design problem, the user has to rely on his experience, previous design, handbooks or trial&error to invent the mechanism, which can then be modelled and analyzed in SAM.
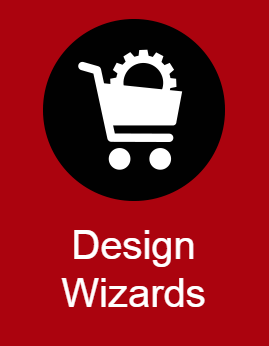
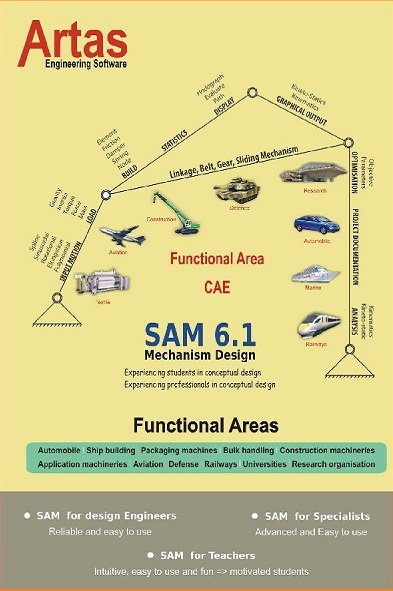
SYLLABUS
- STRENGTH OF MATERIALS
- KINEMATICS OF MACHINERY
- MECHANICS OF MACHINES
- KINEMATICS AND DYNAMICS
- MACHINE COMPONENTS DESIGN
- KINEMATICS AND DYNAMICS OF MACHINES
- DYNAMICS OF MACHINES
BOOKS
- konstruktivegetriebelehre
- Neil Sclater
- WILEY
- DMAGL
- I. I. Artobolevsky
- SAM REFERENCE
- Mechanism Design: Analysis and Synthesis
- Planetenmischer mit dynamisch getriebenen Mischarmen
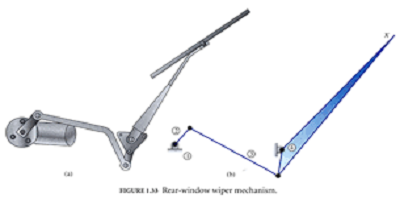
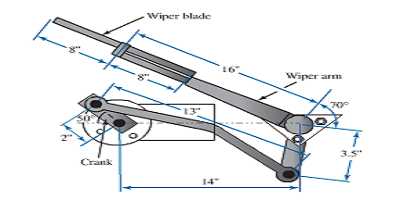
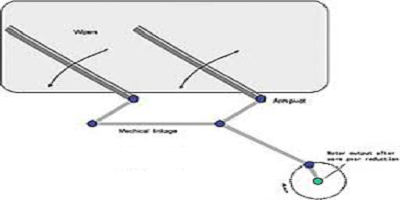
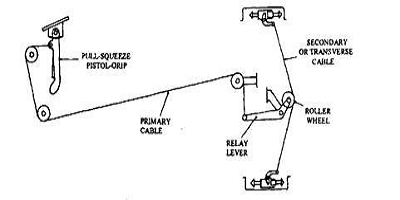
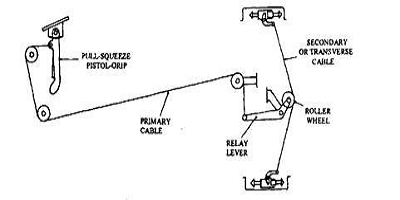
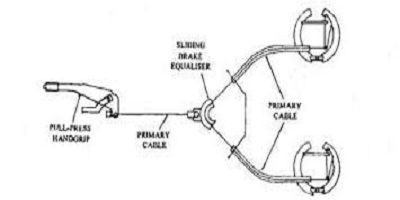
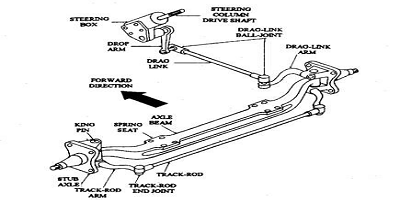
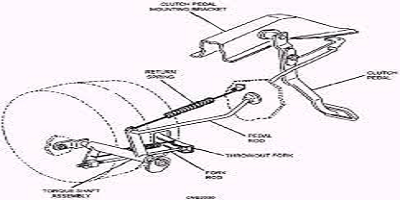
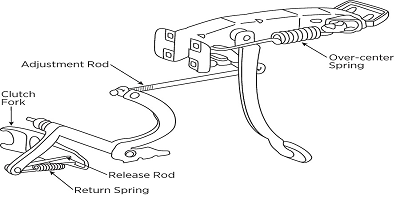
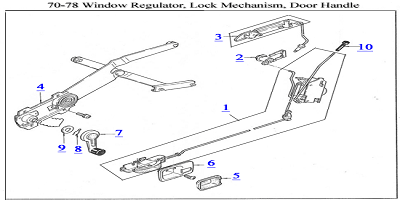
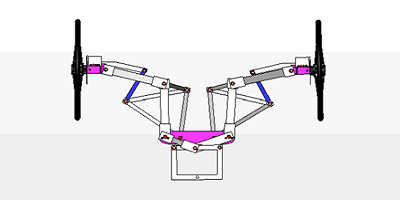
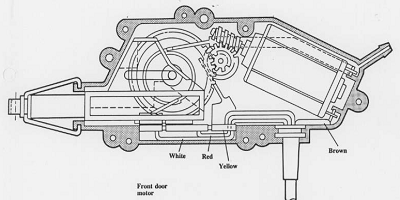
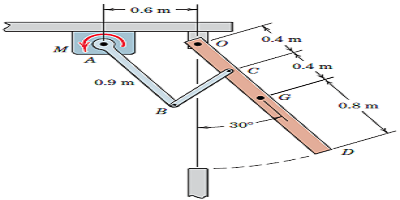
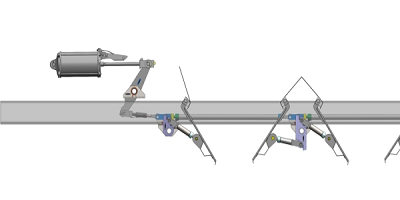
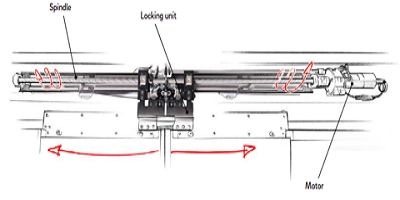
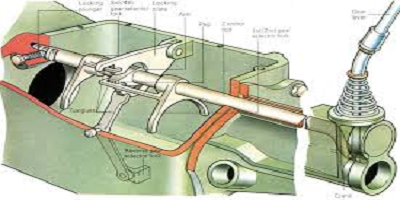
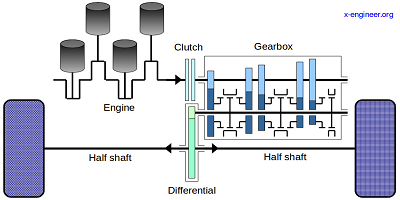
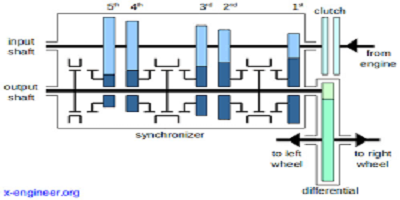
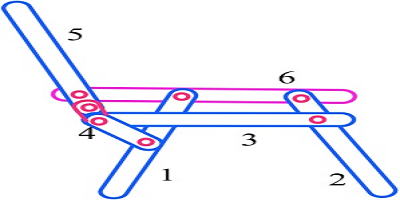
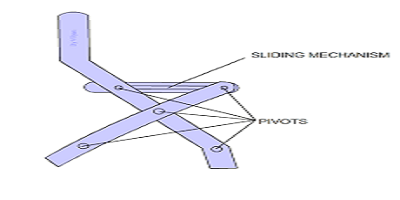
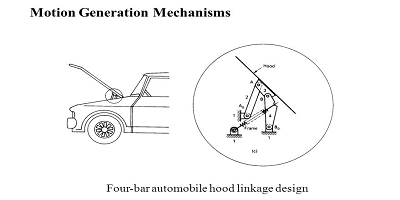
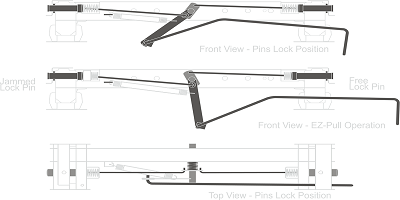
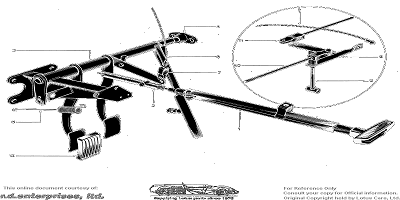
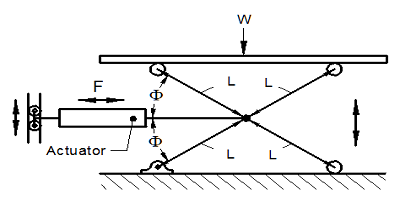
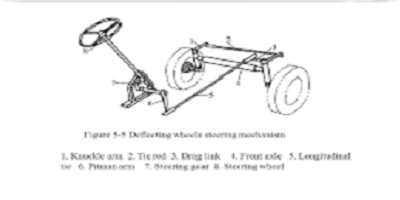
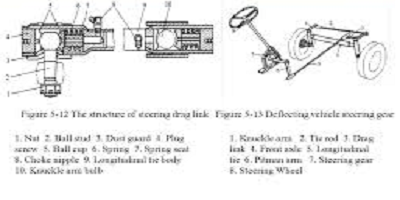
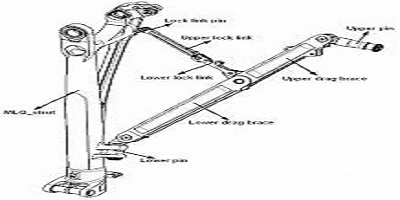
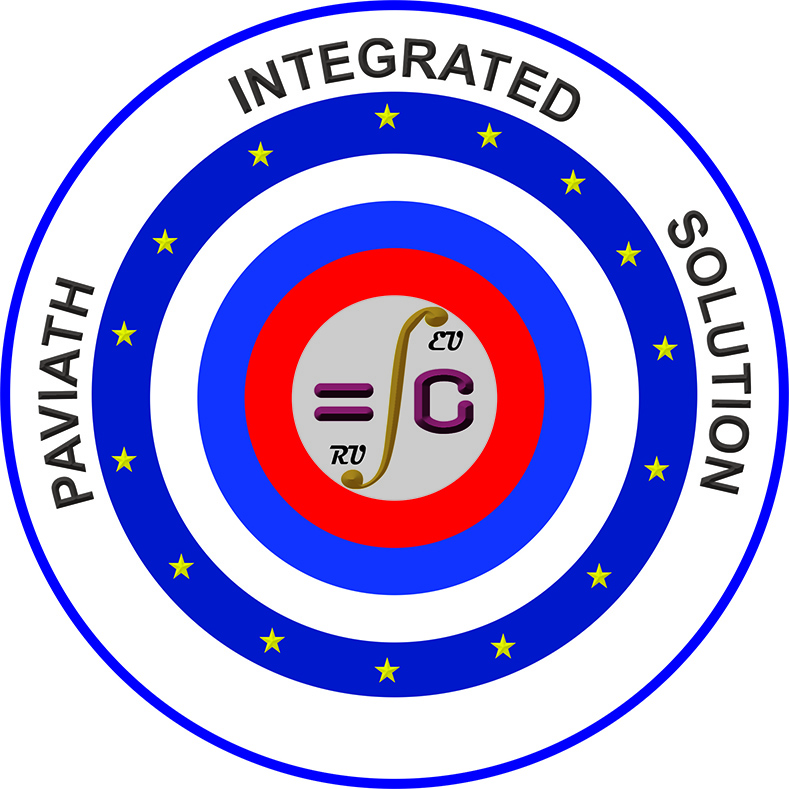
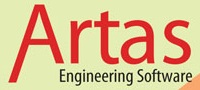
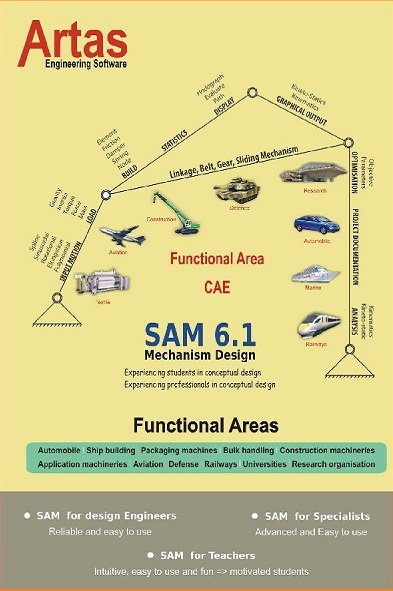
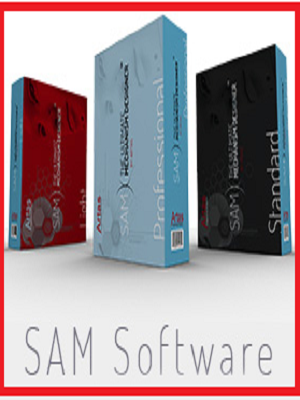