UM Drilling / UM Drillstring Analysis
UM Drilling / UM Drillstring Analysis
Set of specialized tools for solution of scientific and applied problems related to simulation of drillstring / bottom hole assembly behavior in a well. Torque & Drag analysis, Static analysis, Time Domain analysis and etc. functionality is implemented in UM Drilling module within Universal Mechanism GUI and specialized engineering application UM Drillstring Analysis.
UM Drillstring Analysis
UM Drillstring Analysis
UM Drillstring Analysis ENGINEERING SHELL
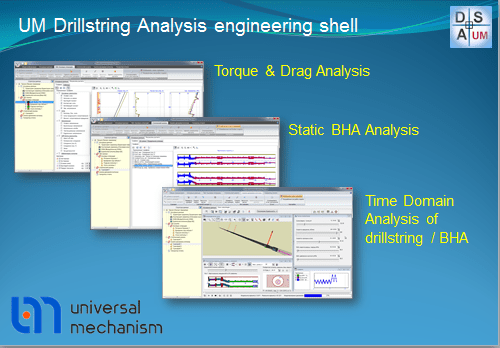
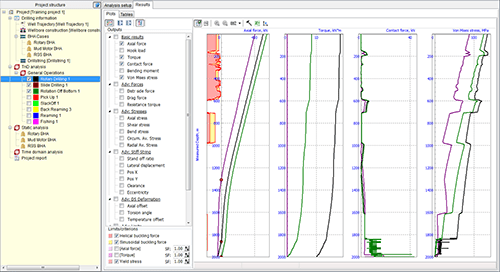
Applied and Research Tasks

“Soft-string” and “Stiff-string” Torque & Drag analysis
Estimation of torque and axial forces acting on drill strings elements in 3D wells for typical operations: drilling, tripping, stuck, rotation off bottom, etc. Calculation of critical loads resulted in sinusoidal and helical buckling of an assembly.
Fast solution of problem within “soft-string” approach and detailed “stiff-string” analysis with account lateral displacements of an assembly in a well are available.
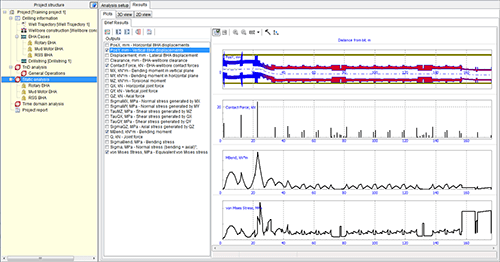
Applied and Research Tasks

Static Analysis
Evaluation of the equilibrium position of the bottom hole assembly (BHA) for the defined bit location in the borehole. The analysis provides an accurate representation of the forces acting on the assembly, as well as internal force factors and stresses acting in the assembly units for various operational cases.

Time Domain Analysis of BHA/drillstring
Time domain simulation of dynamic processes in BHA/total drillstring resulted from bit-rock interaction, side contact of assembly units with wellbore walls, top point rotation control and optional set of forced excitations. Interactive control of model parameters (“point-the-bit”, “push-the-bit” steering, etc.) and operational conditions (hook load or force on top, top point rotary speed, penetration rate, mud flow rate, etc.) during simulation is available.
Applied and Research Tasks

Vibration Analysis
- Linear Vibration Analysis (release at Q4 2021)
Estimation of rotation speeds that can potentially result in damaging vibrations of the Bottom Hole Assembly on the base of linear analysis of an assembly model. The analysis includes evaluation of equilibrium position of the assembly in the wellbore, linearization of equations of motion near the calculated position, evaluation of natural frequencies and modes, as well as linear responses on harmonic excitations for set of rotation speeds.
Critical speed maps are generated on the base of evaluated vibration modes for set of standard excitations of assembly units for list of WOB values (will be available in UM Drillstring Analysis application only).
- NonLinear Vibration Analysis
Time domain simulation of vibrational response of drillstring on set of forced excitations is available within Time Domain Analysis; validation of linear vibration analysis models and results.
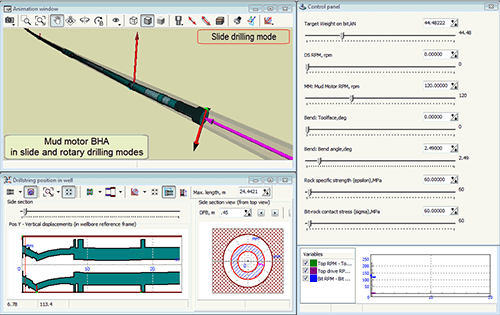
Simulation results can be applied for analysis of an assembly behavior under various operational conditions, transient dynamic effects simulation, verification of linear vibration analysis results, and the choice of optimal configuration and operation modes of drilling equipment.
Directional Tendencies analysis (plan - Q1 2022)
Estimation of directional tendencies of an assembly on the base of estimation of its equilibrium state in the well; iterative prediction of well trajectory on the base of series of numerical experiments.
Applied and Research Tasks




- UM Drillstring Analysis engineering application
The application is generally intended for use by drilling company personnel. The engineering environment provides for setting initial data in a generally accepted format for various types of analysis, launching solvers (including third-party solvers), presenting and comparing results, generating reports, etc.
- Set of tools for engineering support of well design and building, as well as drilling tools development.
- Analogue of Wellplan (Landmark), DrillScan industrial packages.
- Source data description and results presentation in standard drilling engineering format.
- Support of parallel thread calculations and results comparison for multiple set of input parameters (scenarios).
- Automatic report generation routines.
- SI, Imperial, Custom unit system support
Currently, the functionality of the engineering application includes tools for torque&drag, static analysis of the BHA, as well as time domain analysis of assembly dynamics.
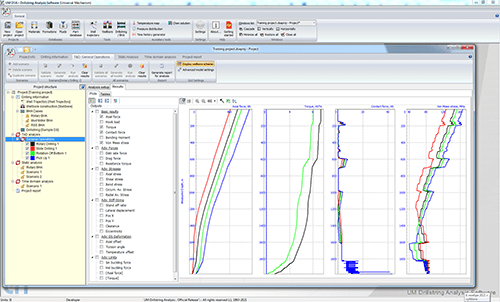
Applied and Research Tasks

- UM Drilling modulus within Universal Mechanism package
UM Drilling modulus provides advanced capabilities in the development and analysis of detailed models of drilling equipment, drillstring–wellbore interaction models, etc. on the base of Universal Mechanism package functionality.
The module is involved to solution of a wide range of research problems within the framework of the Universal Mechanism software package. Along with the standard UM capabilities for description of a model on the base of common library of bodies, subsystems and force elements, the functionality of automatic creation of a model from an engineering description is implemented.
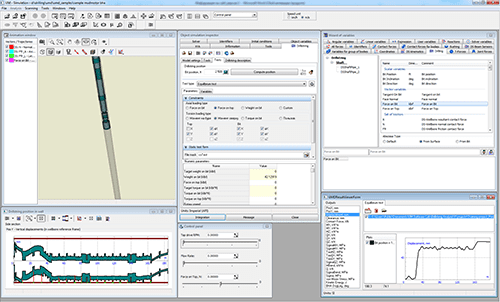


Tools | UM Drillstring Analysis | UM Drilling modulus | CommentH |
Torque&Drag analysis | Estimation of torque and axial forces acting on drill strings elements in 3D wells for typical operations: drilling, tripping, stuck, rotation off bottom, etc. Calculation of critical loads resulted in sinusoidal and helical buckling of an assembly. | ||
Soft String | ![]() | Q1 2022 | Fast solution of problem with simplified model of an assembly. |
Stiff String | ![]() | Q1 2022 | Detailed solution taking into account lateral displacements of an assembly in a well. |
Static BHA Analysis | ![]() | Q1 2022 | Evaluation of the equilibrium position of the bottom hole assembly (BHA) for the defined bit location in the borehole. The analysis provides an accurate representation of the forces acting on the assembly, as well as internal force factors and stresses acting in the assembly units for various operational cases. |
Linear Vibration BHA Analysis | Q1 2022 | Q1 2022 | Estimation of rotation speeds that can potentially result in damaging vibrations of the Bottom Hole Assembly on the base of linear analysis of an assembly model. The analysis includes evaluation of equilibrium position of the assembly in the wellbore, linearization of equations of motion near the calculated position, evaluation of natural frequencies and modes, as well as linear responses on harmonic excitations for set of rotation speeds. |
Directional Tendencies | Q1 2022 | Q2 2022 | Estimation of directional tendencies of an assembly on the base of estimation of its equilibrium state in the well; iterative prediction of well trajectory on the base of series of numerical experiments. |
Time Domain Analysis of BHA/drillstring | ![]() | Q1 2022 | Time domain simulation of dynamic processes in BHA/total drillstring resulted from bit-rock interaction, side contact of assembly units with wellbore walls, top point rotation control and optional set of forced excitations. |
Control Panel | ![]() | Q1 2022 | Interactive control of model parameters (“point-the-bit”, “push-the-bit” steering, etc.) and operational conditions (hook load or force on top, top point rotary speed, penetration rate, mud flow rate, etc.) during simulation. |
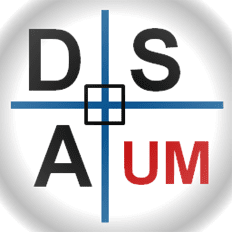
You can edit text on your website by double clicking on a text box on your website. Alternatively, when you select a text box a settings menu will appear. your website by double clicking on a text box on your website. Alternatively, when you select a text box
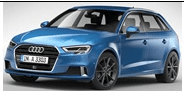
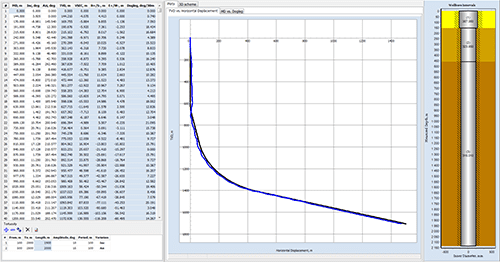
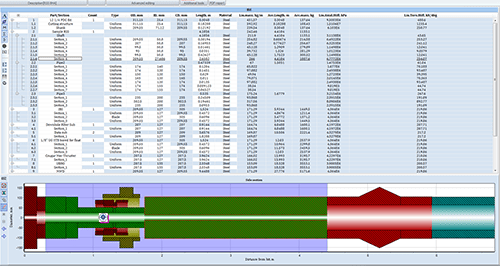
NAFTA region
UM drillstring analysis software is distributed in NAFTA region through our distributor, MindMesh Inc. (www.mindmeshtech.com), under the brand name “RiMo - Well Engineering Software”.
Available functionality: Soft/Stiff String Torque&Drag analysis, Static Analysis, Time Domain Analysis, Hydraulics Analysis (joint development).
Russian Federation, C.I.S.
On the Russian market, our company cooperates with TMK Premium Service division of TMK Company.
“ExpertProDrilling” software is based on UM Drillstring Analysis application and includes Soft String Torque&Drag analysis tools developed in cooperation with TMK.
Within the UM framework the drillstring is modeled by a set of flexible uniform beams, as well as absolutely rigid bodies or FEM models of units of complex geometry, interconnected by joints or force elements. The approach enables description both homogeneous sections of drill pipes and parts of complex configuration: drill bits, stabilizers, mud motors, rotary steerable systems, etc.
Equations of system motion are generated in accordance to the basic multibody system dynamics simulation (MBSD) approach. Arbitrary motion of flexible bodies is considered within modal approach, or by absolute nodal coordinates method. Drillstring model takes into account assembly deformations by it’s placing to the curved wellbore automatically.
The interaction of the drill string with the borehole is described by a set of discrete contact forces of the “circle-cylinder” and “points-cylinder” type. Basic models of bit-rock interaction for roller cone and PDC bits are implemented.
High-performance numerical methods with support for multi-threaded calculations allows efficient solution of BHA/whole drillstring equilibrium state evaluation problem, as well as time domain simulation of assembly motion in wellbore for various operational cases.
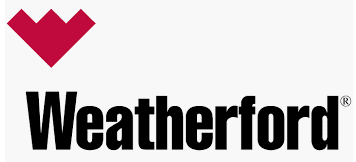
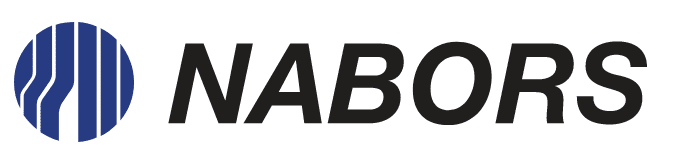
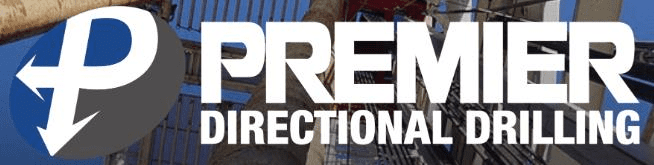
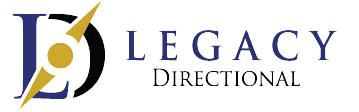