AREAS OF USE
- Engineering
- Defense Industrial Complex
PROCEDURE FOR TECHNOLOGICAL PREPARATION OF PRODUCTION (CCI) ACCORDING TO GOST R 50995.3.1-96 IS DIVIDED INTO STAGES:
- elaboration of working design documentation for manufacturability - technological control of design documentation;
- development of technological processes, technological standardization;
- development of technological equipment and manufacturing processes;
- development of management programs;
- development and implementation of technological processes or the manufacture and testing of an installation series (depending on seriality);
- specification of technological documentation based on the results of development and implementation / release of the installation series.
The requirements for data, the construction of processes and the functionality of systems are rapidly changing. With the proliferation of CNC machines and imported cutting tools, the functionality for calculating cutting modes and transition sizes is less in demand. The operational description is replaced by a route description. The formation of large holdings and the merger of enterprises leads to the appearance of alternative technological processes and data produced by different plants according to the general design documentation. And the implementation of the principles of lean manufacturing leads to toughening the requirements for software flexibility and building systems.
Now few people are interested in the functionality of a single program, the demand for solving problems for the CCI is due to the movement of customer enterprises in the direction of integrated automation. The effectiveness of process data management is considered not only from the standpoint of quality, development speed at each stage, but also from the standpoint of well-coordinated interaction of departments, the level of system integration, strict adherence to work schedules, and process optimization at the interface of software environments. A key role in meeting the requirements in view of the current situation is played by the PDM system, which should provide the solution to the problems of project management, archive management and data integrity control, distribution of rights, change management, integration of CAD / CAM / CAPP class systems, as well as further data transfer to ERP and MES systems. *
The basis of effective management is a work plan. Planning is carried out in the planning and management system for production preparation as part of the LOTSMAN: PLM. When forming plans, the time limits are set, the executors, previous tasks, the data necessary for development are placed on the input, and the finished result is output, which can be agreed upon by automatically starting the business process associated with the task. As a result, monitoring the implementation of plans becomes simple and convenient. PILOT: PLM allows you to create plans automatically. For example, if you have a service for re-assembly and distribution of responsibility for the development of a technical process between specialists by type of work (machining bureau, assembly bureau, etc.), you can automatically draw up a work plan based on the data from inter-workshop technological routes.
WORK PLAN
Work plans for the development of control programs and tooling design divisions are automated based on the data of approved applications for UE and STO. Development of the working design for manufacturability is carried out in the PDM system as a stage of approval of the design documentation.
The technologist receives a task in the system for approval with the attached set of CD. Documentation annotation options are available for work using the secondary presentation and PDF processing tools.
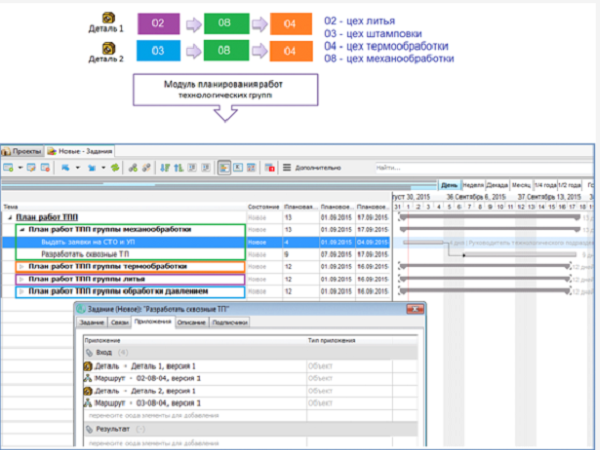
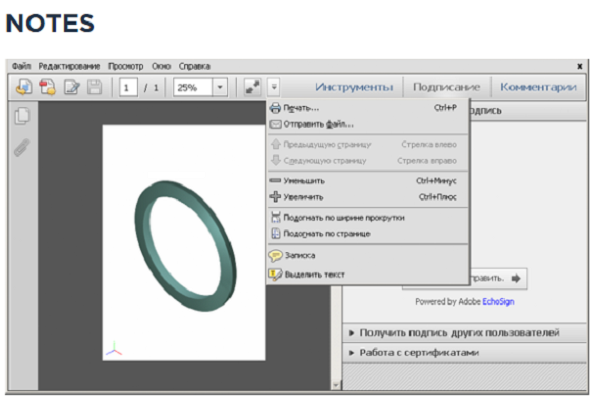
Notes can be left with the digital “red pencil” or recorded in voice.
Formation of the production and technological structure of the product, inter-workshop technological routes, preliminary determination of resource requirements, the formation of summary statements are provided by means of the LOTSMAN system: PLM and its applications. The principles of building a system depend on the availability of these tasks at the enterprise.
The development of technological processes is carried out in CAD software VERTICAL. The system allows you to develop single, standard and group technological processes for various types of production with any degree of detail in an integrated environment convenient for the technologist.
MECHANISM OF INTERACTION
The functionality of the system allows you to embed VERTICAL into the overall design process and an effective interaction mechanism.
Firstly, data from the designer, previously made in KOMPAS-3D, is automatically loaded into the CAD / C VERTICAL technological process: 3D model, drawing, DSE parameters (designation, name, weight, etc.) and material from the drawing are transferred, as well as data on picking and procurement (if the norms of material consumption were calculated even before the development of TP). This approach allows you to use the mechanisms of associative work and parameterization, as well as to eliminate errors in entering information and to optimize the time costs.
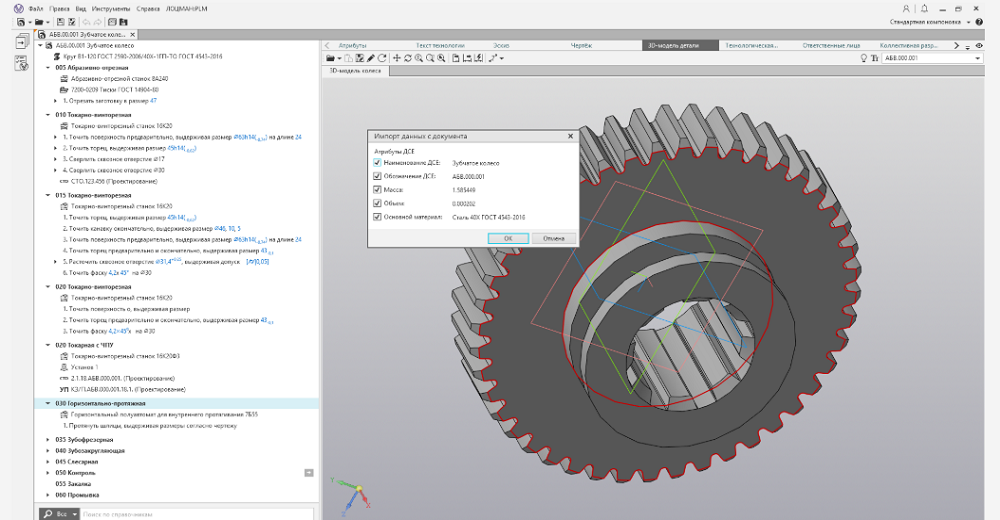
Secondly, the selection of data is carried out from the corporate directory of the technologist using filters and automatic data selection, which allows for a unified interpretation of the resources described in the technological process in both PDM and ERP systems. Configured links between directories, work with fragments, typed operations, and a knowledge base of cutting modes (the functionality that is relevant for automatic selection of modes using an imported cutting tool in a TP) allows optimal data selection.
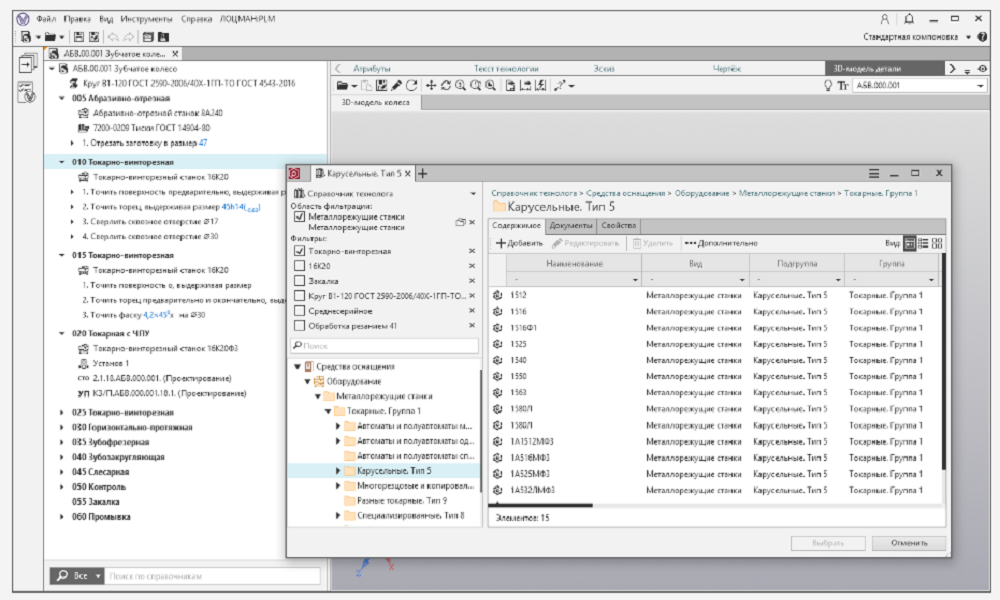
Thirdly, in the development of technological processes, teamwork tools are used, which ensures user interaction in solving related problems, namely:
- it is possible to transfer the CNC operation to the development by the programmer and save the control program in the context of the CNC operation;
- when differentiating responsibilities between technologists for the development of technical specifications for different technological conversions in the technological process *, you can create a link to another technical specifications, thereby ensuring the “collectability” of the end-to-end technological process.
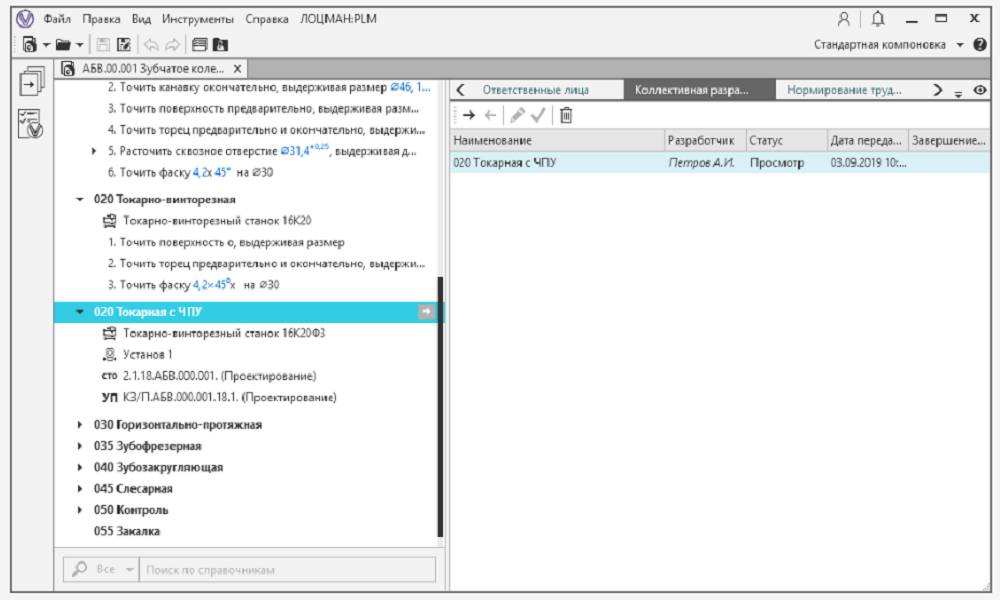
COMMUNICATION OF TP DESIGN PROCESSES
Fourth, in terms of interaction with equipment design services and development of control programs, it is possible to create an application for service stations and UEs in the form of an enterprise directly when designing TPs, the stages of approval of the application are monitored in real time. This ensures a connection between the processes of designing TP, as well as the design of equipment and development of UP.
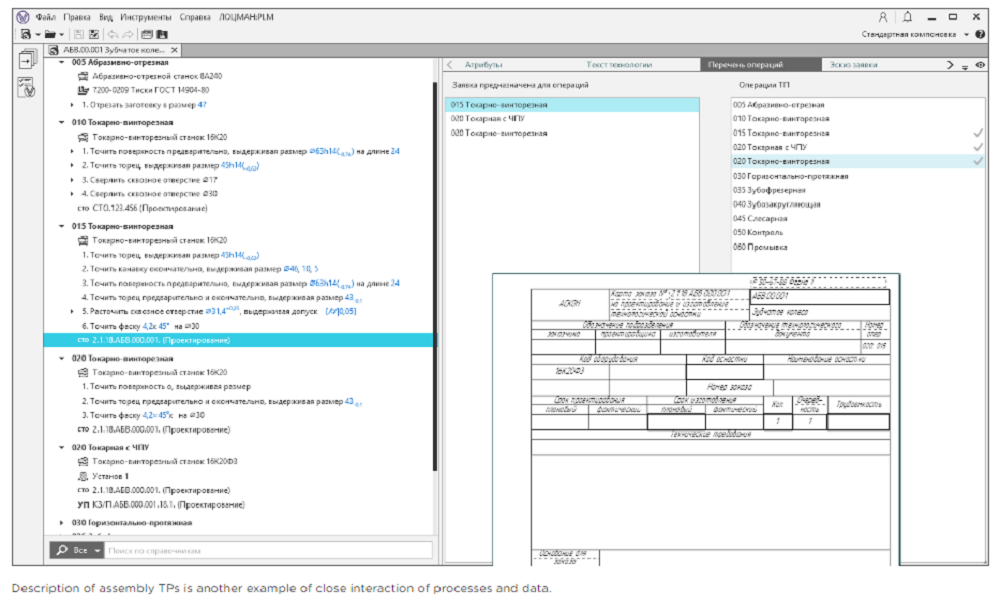
Description of assembly TPs is another example of close interaction of processes and data.
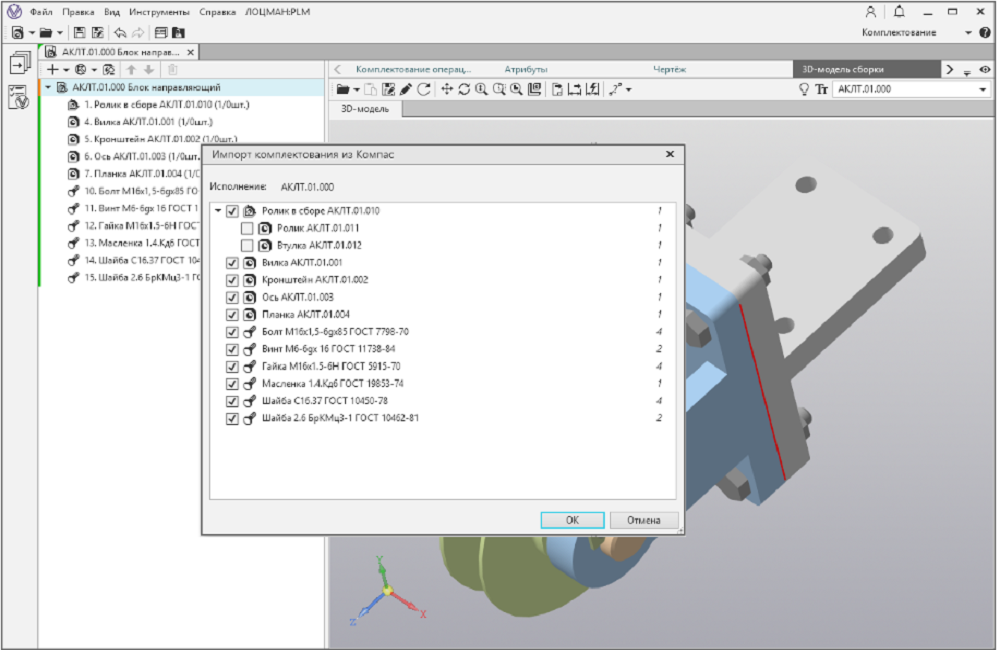
At TP operations, components of the product structure (production, technological or structural) stored in the PDM system are used as components, verification mechanisms are applied, and data on components during operations while saving TP appear in the structure of the electronic process technology. Consequently, in the production system, information on providing workshops, sections and jobs with components will be transparent.
Version and change management is carried out in close conjunction with PDM-SAPR TP, which allows not only to provide the necessary information protection, but also to automate the registration of data on changes in the TD set, as well as minimize the number of reprinted sheets.
After the development of the technical process, the technologist can automatically check it:
- according to reference data, which is a convenient mechanism for updating and revising TP, because it allows you to identify remote, changed and not used NSI objects;
- according to technological data for compliance with the requirements of normative control (the algorithm is configured);
- for compliance with the inter-workshop technological route.
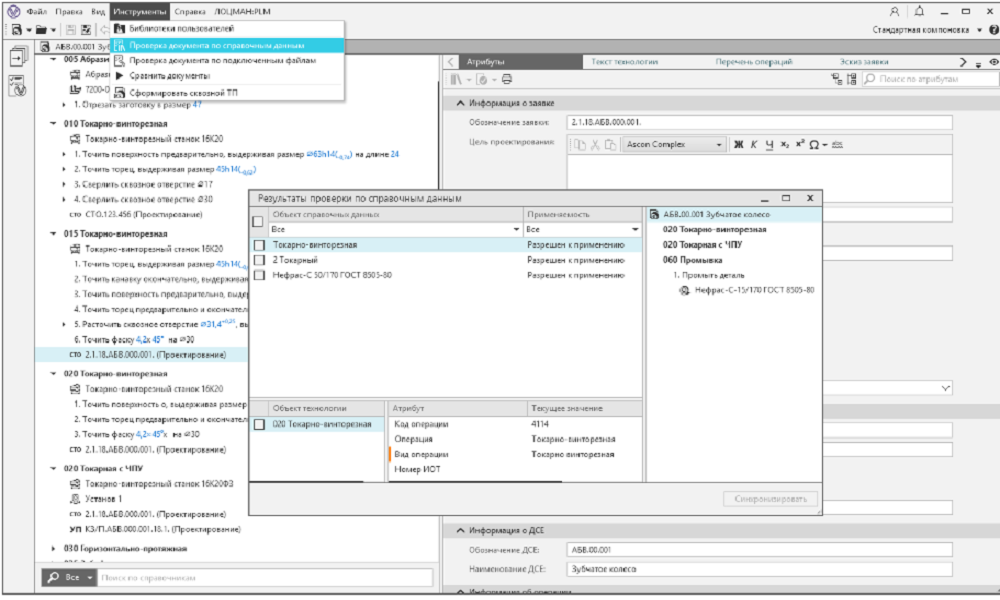
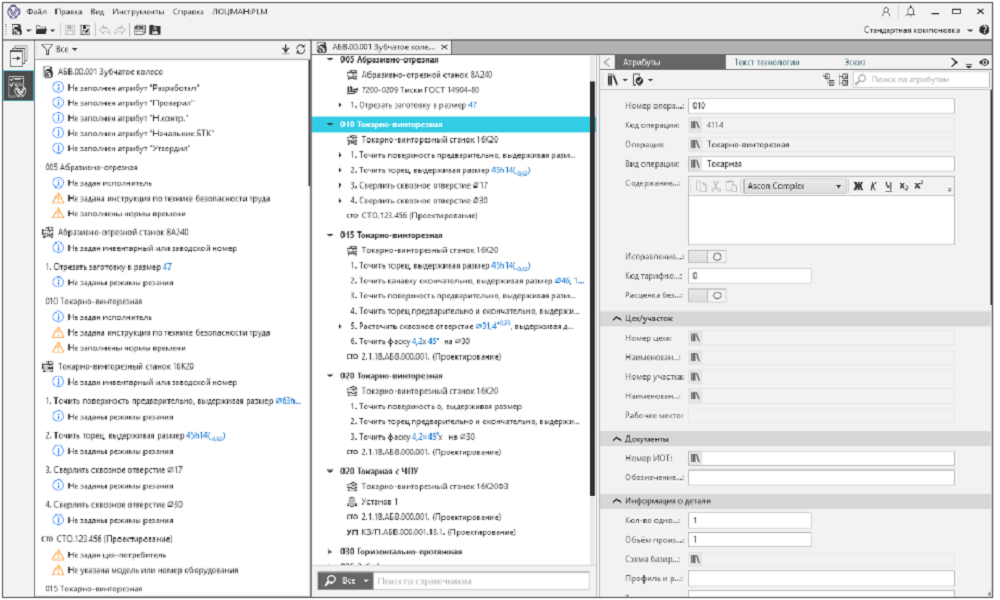
As a result, at the exit while maintaining the process technology we get:
- automatically built and stored in the LOTSMAN: PLM technical process that describes all the resources necessary for the production, which, after rationing and approval, is transferred to the production system for production planning, management of production and processing facilities (production specifications) and accounting;
- a set of technological documentation for ESTD or STP, generated automatically.
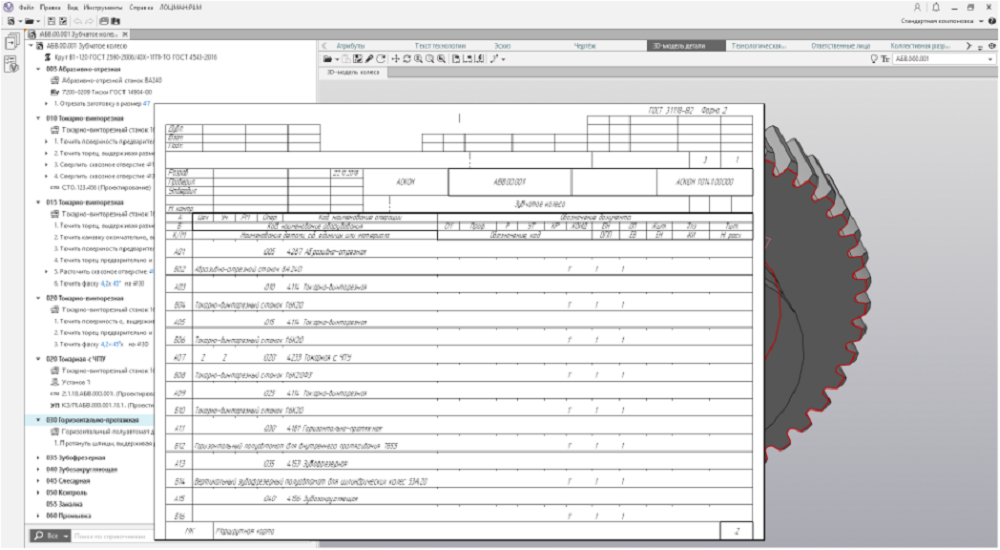
Rationing of operations of the technological process, the final stage of development of TP, is carried out in the application Rationing of labor costs. Rationing can be carried out both according to inter-industry and general machine-building time standards, and using the time norms obtained from the CAM-environment or calculations.
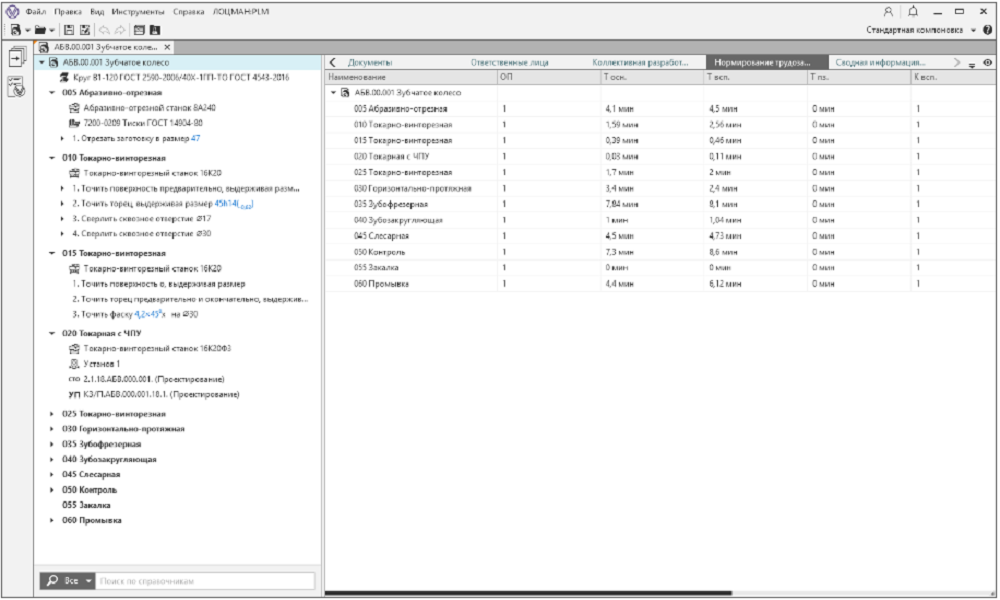

The settings of the system and applications of CAD software VERTICAL allow you to adapt it for the production of various products of various types of production (single, serial, mass), use by different groups of specialists and for work in accordance with new quality standards.
DESIGN STAGES
One of the stages of the CCI - the design of technological equipment - is implemented on the basis of a plan built on requests from technologists. Tools for the design of service stations are the same as in the development of products of the main production.
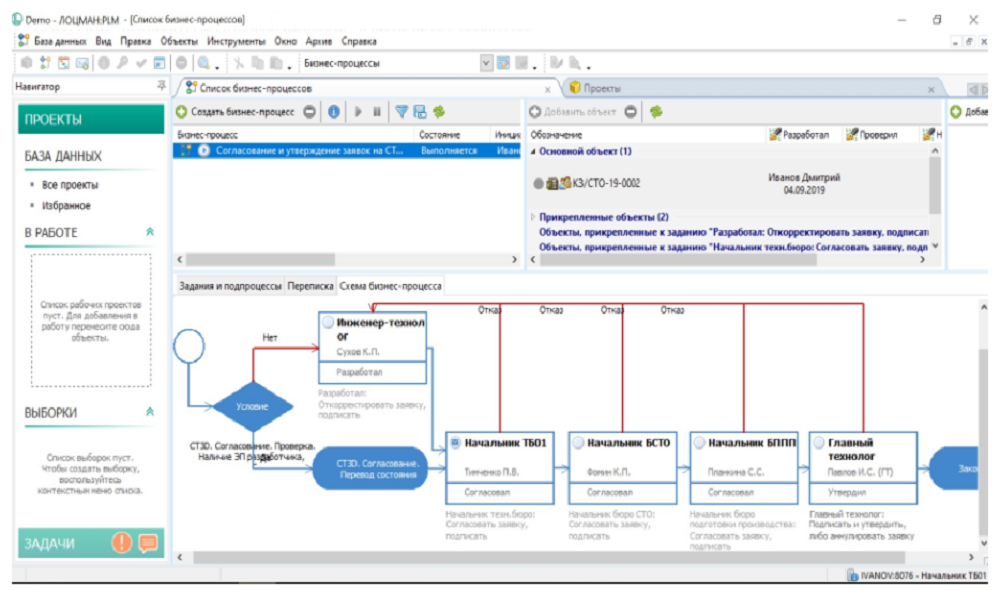
The newly designed snap-in is registered in the Technologist’s Handbook of the business process, and data on its designation and name are available to the technologist for inclusion in the technological process. Methodically and functionally, the process “technology - application - plan - design - approval of design documentation - a new NSI facility - equipment in technology" is provided, and, of course, the designed service station should be transferred to the production system to manage the production upon approval of all data.
The development of management programs (UP) is one of the most critical stages of the CCI. Its management, as before, is carried out on the basis of a plan consisting of tasks, at the input of which there is an application for a control unit, a 3D model, and a description of the operation with the CNC.
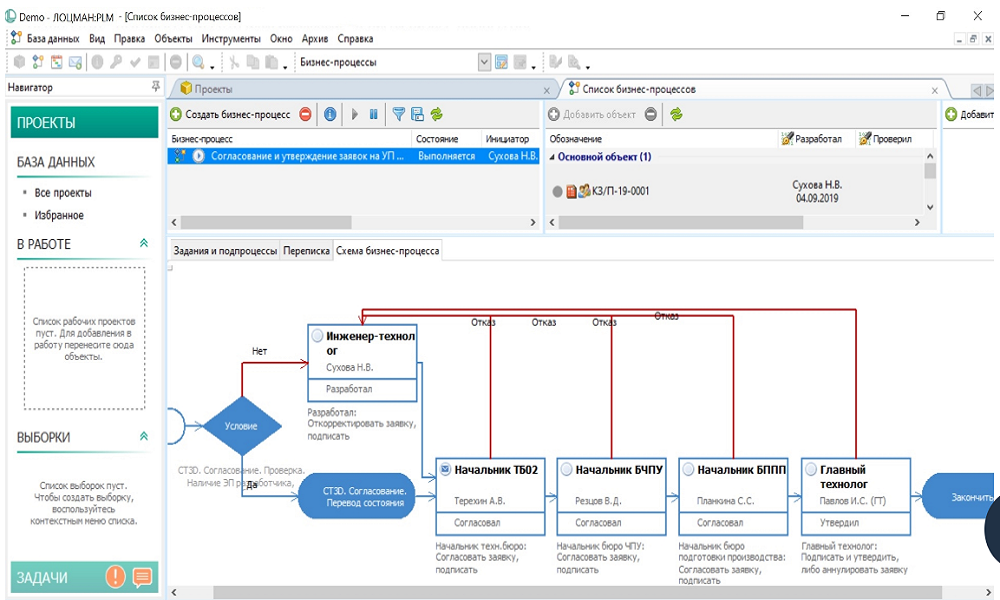
The three-dimensional model can be rebuilt by the technologist in the middle of the tolerance field, adapted for the development of UE and visualization, snap-in and equipment elements can be added to it to eliminate possible errors and, as a result, costs. The CAM system selected by the enterprise is responsible for the development of control programs, however, the files and the result — UP — are stored in a single environment, undergo approval, approval, and implementation procedures. Coordination and approval of any data is carried out using the LOTSMAN mechanisms: PLM WorkFlow and standard business processes, and typical business processes themselves are built in accordance with the approval schemes adopted by the enterprise.
The development, implementation and release of the installation series - production tasks, the refinement of the data according to the results takes place in the LOTSMAN: PLM - VERTICAL link with execution of implementation certificates and other related documents.
PROCESS CHAIN
Technological preparation of production is not only the development of technologies and their rationing, but also a chain of interrelated processes characteristic of a particular enterprise. PILOT: PLM acts as the central link of the end-to-end chain responsible for the interaction of users and systems.
CAD TP VERTICAL, KOMPAS-3D and applications for technological preparation of production are the tools of the technologist intended for the development of the technological process. These systems are closely interconnected and are tuned to the processes of the enterprise.
THE SOLUTION IS IMPLEMENTED ON THE BASIS OF PRODUCTS
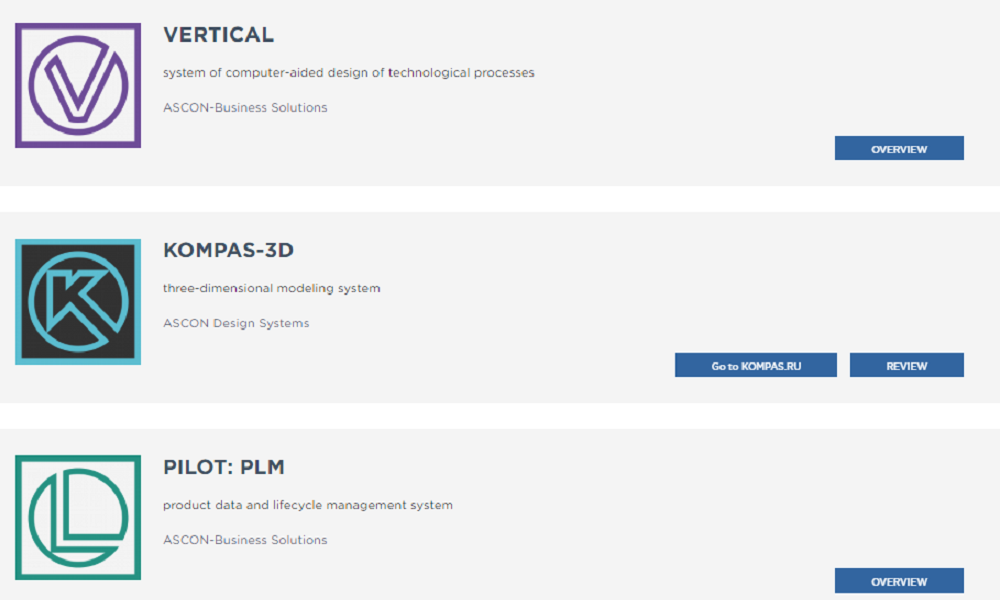