UM Durability
UM Durability
Fatigue analysis (UM Durability)
General information Introduction to UM Durability - Workflow diagram - Example: locomotive bogie frame and long-wheelbase flatcar - Download presentation
General information
This page describes the CAE-based durability analysis that is being implemented in Universal Mechanism software to predict the fatigue damage of parts of mechanical systems. The dynamic simulation of parts is performed using Universal Mechanism. Flexible body representation is considered using external finite element (FE) software. The present version of UM supports the following FE software: ANSYS and MSC NASTRAN. The final durability post-processing analysis is performed using the UM Durability module.
The analysis starts with the dynamical hybrid model in Universal Mechanism. The flexibility characteristics of the structural parts are incorporated into UM model using a modal formulation based upon component mode synthesis. Basically, this method represents the part's flexibility using a modal basis, which is optimized to account for constraint and force locations. The mode shape displacements and stresses are calculated using the finite element software.
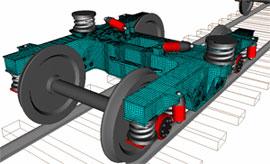
The UM Durability module combines the stress time history information generated during series of numerical experiments in UM and the material fatigue strength characteristics to generate the predicted life distribution in the part.
Any durability analysis relies on three key inputs. There are 1) Time history of the stresses at any point in the structure and 2) Material data - how the material reacts to repeated stress application at various stress levels.
By employing the full finite element representation of the component in the UM model, the local stresses are directly obtained as result of the UM solution. In the UM FEM module, flexible body deformations are modeled as a linear combination of mode shapes. As long as the number of mode shapes selected adequately the modal superposition will model deformations accurately and efficiently.
When UM Durability is started, the user is prompted for the location of modal coordinate time history files and orthonormalized mode shapes files, then the type of analysis required and the material data to be used.
With all of the parameters set, UM Durability performs the stress at every node, and then proceeds to multi channel peak/valley extraction and rain flow cycle counting, followed by the damage sum.
The idea that the deformation of a flexible body can be represented by the sum of a number of mode shapes, scaled by appropriate factors, can be extended to stresses in the body as well. These factors, or modal coordinates, can be used as the scaling factors on the stress solution of each mode shape and the superposition of these scaled stresses represents the body's instantaneous stress state. If the superposition is performed at every node in the finite element model, for every time step in the UM solution, the stress time history is defined at every location.
Using the UM FEM tools the modal coordinate time history can be saved for every numerical simulation in UM. Based on this modal time history and file with orthonormalized mode shapes from ANSYS or MSC NASTRAN the stresses at every node can be obtained.
When UM Durability is started, the user is prompted for the location of modal coordinate time history files and orthonormalized mode shapes files, then the type of analysis required and the material data to be used.
With all of the parameters set, UM Durability performs the stress at every node, and then proceeds to multi channel peak/valley extraction and rain flow cycle counting, followed by the damage sum.
Introduction to UM Durability
Estimation of long-time strength of construction elements is one of the principle problems taking place during new machines and mechanisms designing. Main factor bearing to the durability of machine parts is a mechanical loading.
Present-day methods enable to make durability estimation in the presence of source data, including fatigue resistance properties of the detail, determined with constructional, technological and operational factors, and detailed description of operational conditions of the detail. Estimation method specifies fatigue resistance properties source data format; full-length operational conditions data contains records of stress-strain stage changing history of the detail, presented in the form of stress loading half-cycle sequence.
Experimental research of stress loading of the detail involves necessity of pre-production model manufacturing. Therefore it cannot be hold at the early stages of mechanism designing. Computer-aided investigation has not this disadvantage and permits to reach a considerable economy of time and resources.
Let,s view the procedure of CAE-based stress loading and durability analysis that is being implemented in Universal Mechanism software to predict the fatigue damage of parts of mechanical systems.
- Operational conditions of the mechanism are described with the number of particular load cases.
- Hybrid models of the mechanism, including strength investigated details as flexible bodies, are created with the means of UM FEM module.
- Numerical experiments for all the selected load cases are hold. Modal coordinates time-histories for all the flexible bodies are evaluated and saved for every numerical simulation. Series of numerical experiments can be held with the means of UM Experiments module. Simulation results are exported to UM Durability module.
- Durability analysis is hold for a single detail. With the means of UM Durability module groups of sensors (nodes of finite element model of the detail) are described. Based on records of previously calculated modal coordinate time-histories, stress realizations for each sensor for every load case are evaluated. These realizations are schematized for the further durability analysis; their statistical properties are used for the preliminary search of control areas of the detail.
- Preparation for durability analysis includes selection and setting parameters of the method, relative parts of load cases per life-time unit setting and fatigue resistance properties for control areas description. Durability and accumulated damages are estimated for each control area in case of single load case and in case of load case combination.
Current UM Durability version includes durability prediction algorithms for multi-cycle fatigue, which accord to the regularities of Russian locomotive building, carriage engineering, and their modifications.
The UM Durability module supports:
- Stress loading and durability evaluation results visualization and export to external programs;
- Graphical representation of stress loading and durability evaluation result distributions;
- Add-able fatigue resistance properties of construction materials guide.
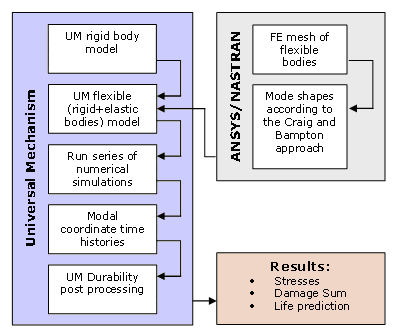
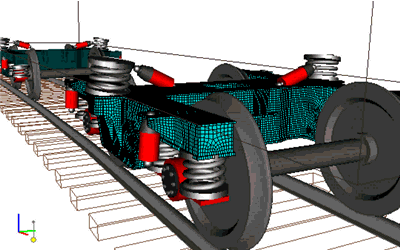
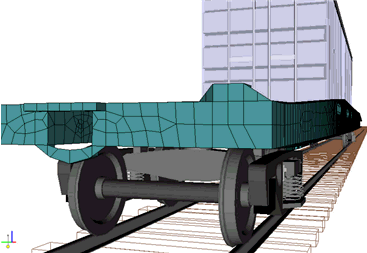
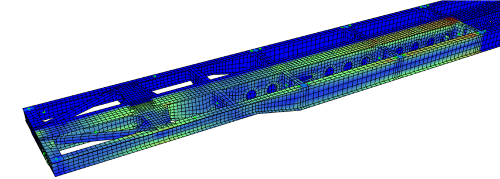
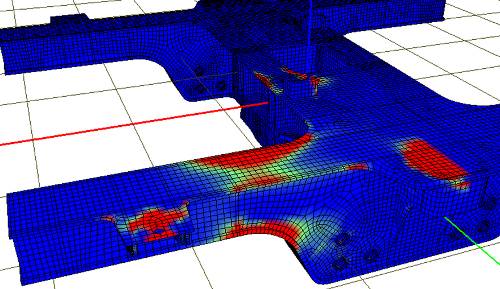
locomotive bogie frame and long-wheelbase flatcar