8D. Quality control
The topic of product quality assurance is relevant for each enterprise. The modern organization of production provides for the mandatory presence of a quality management system, one of the main goals of which is to ensure the release of quality products.
This is achieved by system processes and procedures that must operate on an ongoing basis. To increase the efficiency of these processes and, as a consequence, to improve product quality, the principle of continuous improvement should be applied - PDCA
According to the PDCA principle, to improve the process, it is necessary to determine its current state, which will be the starting point for further improvements. In the case of quality, this is an objective picture of the quality of products in each division of the enterprise.
If an enterprise has problems with product quality, it is not a fact that the reason lies with the competence of personnel who make the wrong decisions. Perhaps management decisions are not based on objective data. And so the activity is chaotic and does not bring the desired result.
The product “8D. Quality Management” will help solve problems in the field of collecting and analyzing information in order to obtain a basis for making decisions on improving quality.
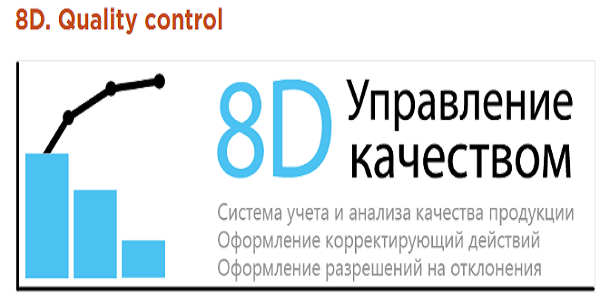

The system performs the following functions
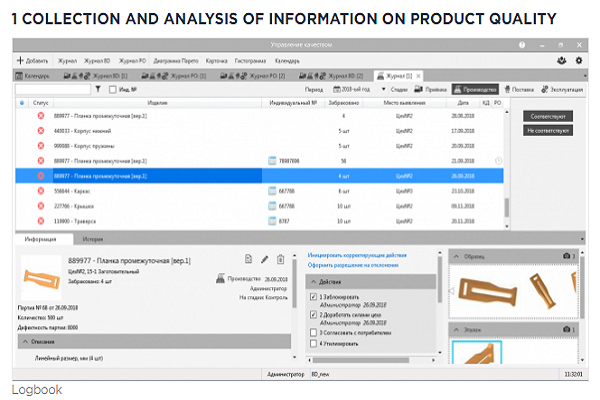
Analytical tools allow you to answer a number of pressing questions:
- which supplier supplies the most defective products and which?
- which workshop, site, equipment or contractor produces the largest amount of non-conforming products?
- Top 10 reasons why non-conforming products arise in production?
and many others.
The results of the analysis can be used to develop a program to improve product quality.
The following life cycle stages are supported:
- acceptance (incoming quality control);
- production;
- delivery (quality control is carried out by the consumer in his company);
- warranty (warranty and post warranty operation)
The array of information in the journal must be processed, so our system contains a number of tools for analyzing statistics on product discrepancies.
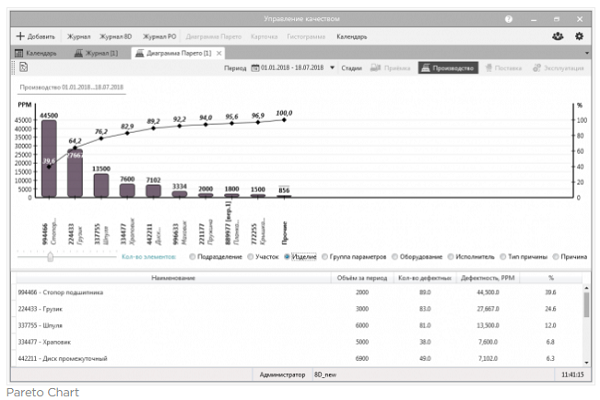
2 ACCOUNTING FOR QUALITY PRODUCTS
The system allows you to take into account the results of all methods for determining the conformity of products to requirements. And if it is possible to initiate corrective actions or a permit for deviation when identifying inappropriate products, then the positive results of control, measurement, testing can be used in the formation of an electronic passport of product quality.
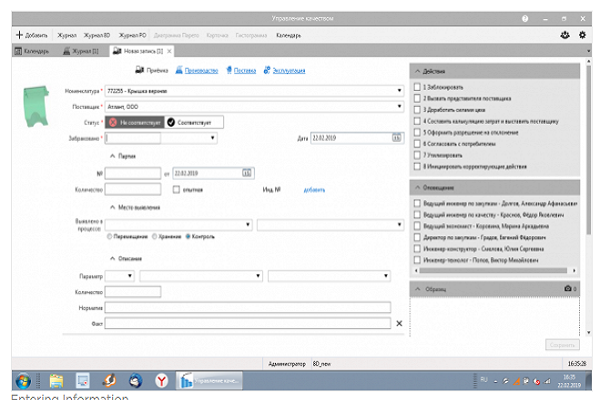
Thus, having received a sample of information on the quality of a specific product instance (by serial number), it is possible to obtain a report that will be objective confirmation that the product meets the requirements, and therefore is of high quality.
Main functions:
- administration of corrective actions (control of deadlines);
- displaying a list of tasks for a specific performer for all open corrective actions;
- storage of all documentation that arises as a result of solving the problem;
- tracking the effectiveness of corrective actions.
Application of the system will make it possible to implement the requirements of the standard and make corrective actions at the enterprise traceable and manageable.
3 CORRECTIVE ACTION
This is a mandatory procedure of any quality management system (business). It is used to eliminate the consequences and causes of non-compliance. The complexity of the implementation of the procedure lies in the large number of participants and stages. If several corrective actions are open at the same time, then it is necessary to monitor the implementation of many stages and coordinate the work of units in the framework of solving quality problems.
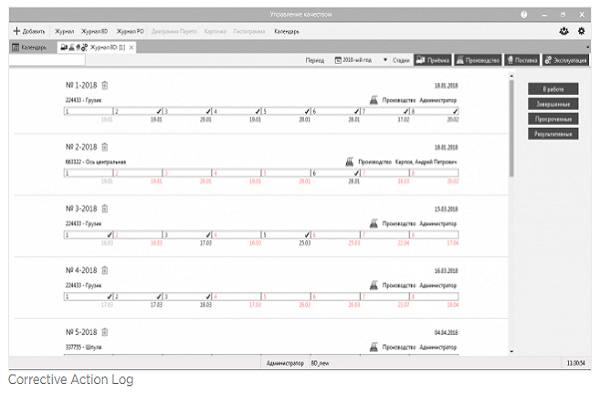
The product uses the 8D corrective action technique, which has already proven its effectiveness around the world. The procedure is based on 8 stages, which from each problem allow you to actually create a case for its solution.
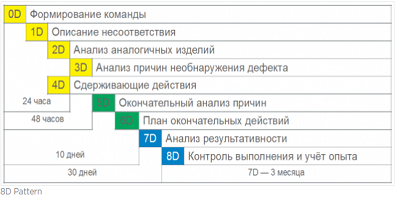
4 PERMISSION FOR DEVIATIONS
The procedure allows authorizing the use of products with deviations in production. Used in cases where corrective actions are not possible. An expert team is created in the system, each member of which expresses his opinion on the admissibility of using products with deviations. The final decision maker examines the opinion of the team and makes a final decision.
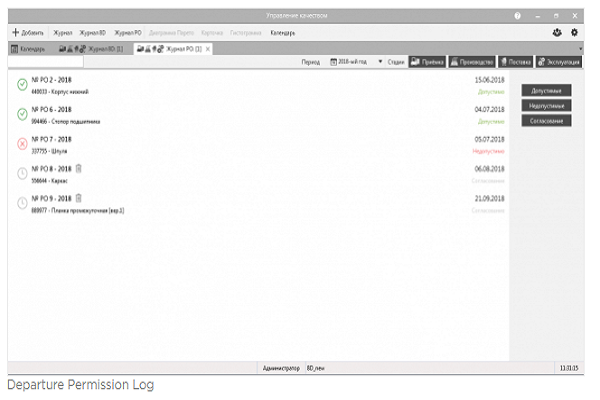
Using the system will make the process of issuing permissions for deviations traceable, record the decisions of responsible persons and use each case of registration as a case in the knowledge base of the enterprise.
5 ENTERPRISE KNOWLEDGE BASE
Filling the system with information about inconsistencies, problems and their solutions in the form of corrective actions and permissions for deviations, you thereby form the knowledge base and experience of your enterprise.
When identifying another quality problem, it will be possible to turn to the knowledge base and obtain information on how to solve a similar problem.
In addition to reducing the time to solve problems, the system will allow to fulfill the requirements of quality standards related to the formation of the organization’s knowledge base.
You can try the product for free for 45 days. To do this, go to the product website and fill out the form.
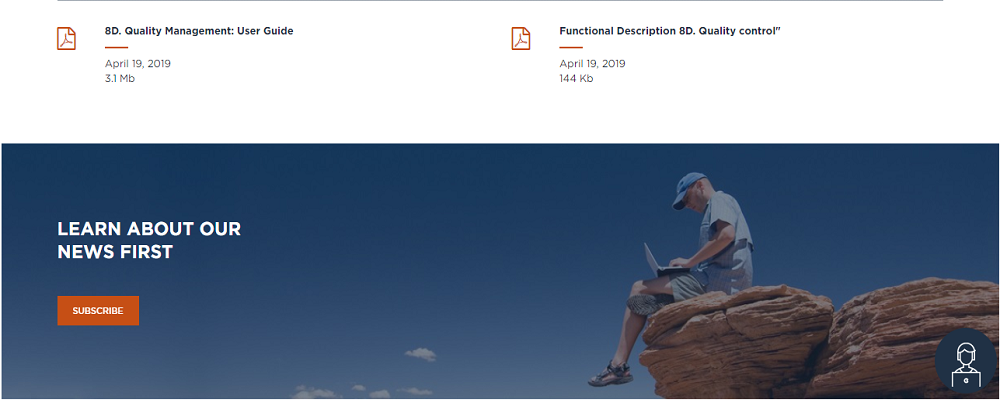
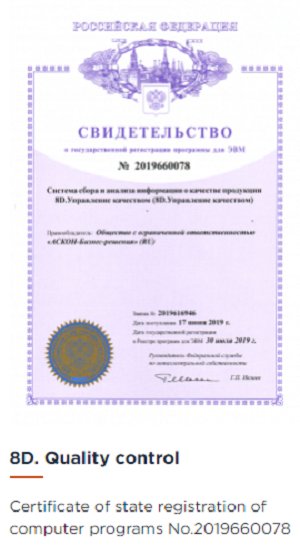