APM FEM
The system of strength analysis APM FEM for KOMPAS-3D
APM FEM is a strength analysis system designed to work in the interface of the Russian CAD system KOMPAS-3D.
The main purpose of the system is to enable the designer, already at the initial stages of design, to make correct and well-grounded design decisions using the constructed 3D models. This undoubtedly improves the quality and saves time spent on product development, and therefore makes it competitive!
Typical objects for calculation are parts and assemblies that are small in terms of the ratio of overall dimensions and wall thicknesses: rods, lugs, stops, brackets, corners, levers, body parts, supporting elements, etc. For such parts and assemblies, it is important to QUICKLY assess the strength of the elements with possible design optimization, using the associative relationship of the geometric and calculation models.
The main steps in the calculation:
- Preparation of a 3D model for strength analysis (geometry simplification);
- Analysis and setting of boundary conditions (loading, fixing);
- Automatic generation of a finite element mesh on a 3D model;
- Selecting the required type of calculation and setting its parameters;
- Calculation;
- Viewing the results obtained and analyzing the values ​​of the main design characteristics (stresses, safety factors, displacements, etc.);
- Modification of the model based on the results of the calculations (change of geometry / material);
- Re-performing the computational analysis to confirm the performance of the product.
- Calculation of surface models (shells) This
option allows you to calculate surface models created in KOMPAS-3D. In this case, meshes of lamellar finite elements are used. - Topological optimization This
option allows you to carry out a design calculation in order to determine the optimal distribution of material to improve the mass-stiffness characteristics of the product
The APM FEM product is registered in the Register of Russian computer programs and databases.
In addition to the basic capabilities, additional functionalities (options) are available for the product :
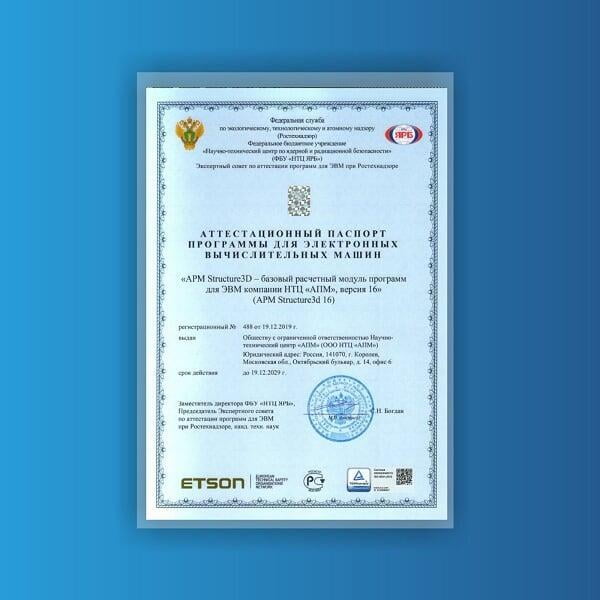
SOFTWARE CERTIFICATION PASSPORT 2019 This attestation passport establishes the purpose and scope of the APM Structure 3D software tool.
This attestation passport establishes the purpose and scope of the APM Structure 3D software tool.
SOFTWARE CERTIFICATION PASSPORT 2013 This attestation passport establishes the purpose and scope of the APM Structure 3D software tool.
This attestation passport establishes the purpose and scope of the APM Structure 3D software tool.
Working documentation
The section contains the current documentation for the operation of APM FEM:
The minimum system requirements for APM FEM work meet the requirements of KOMPAS-3D.
KOMPAS-3D is intended for use on personal computers such as IBM PC running Russian-language (localized) or correctly Russified operating systems:
- MS Windows 10,
- MS Windows 8.1,
Microsoft .NET Framework 4.5.2 or later must be installed on the computer.
A prerequisite for the operability of KOMPAS-3D and configurations is the support by the central processor of instructions not lower than SSE2.
For other parameters, the minimum possible computer configuration for installing and running KOMPAS-3D meets the minimum system requirements for the corresponding operating systems.
When installing KOMPAS-3D, keep in mind the following:
- the bitness of the KOMPAS-3D version must correspond to the bitness of the operating system version, that is, 64- or 32-bit KOMPAS-3D can be installed only on a computer with a 64- or 32-bit OS, respectively;
- to work with the 64-bit version of KOMPAS-3D, it is recommended to use a computer with a multi-core processor and at least 8 GB of RAM.
The rest of the hardware requirements for the 32- and 64-bit versions of KOMPAS-3D are the same.
The recommended monitor resolution is 1920 x 1080 pixels or more.
APM FEM is a strength analysis system designed to work in the interface of the Russian CAD system KOMPAS-3D.
The main goal of the system is to enable the designer, at the initial stages of design, to make correct and reasonable design decisions using the built 3D models. This undoubtedly improves the quality and saves time spent on product development, and therefore makes it competitive!
Typical objects for calculation are small in terms of the overall dimensions and wall thickness of the part and assembly: thrust, lugs, stops, brackets, angles, levers, body parts, support elements, etc. For such parts and assemblies, it is important to QUICKLY evaluate the strength of the elements with possible optimization of the structure using the associative connection of the geometric and computational models.
The main steps in the calculation:
- Preparation of 3D-models for the calculation of strength (simplified geometry);
- Analysis and setting of boundary conditions (loading, fixing);
- Automatic generation of the finite element mesh on a 3D model;
- Selecting the required type of calculation and setting its parameters;
- Carrying out the calculation;
- View the results and analyze the values ​​of the main design characteristics (voltages, safety factors, displacements, etc.);
- Conducting a modification of the model according to the results of the calculations (change of the geometry / material);
- Repeated computational analysis to confirm the performance of the product.
The product APM FEM is registered in the Register of Russian computer programs and databases .
In addition to the basic features, additional functionalities (options) are available for the product :
- Calculation of surface models (shells)
The option allows the calculation of surface models created in KOMPAS-3D. When this mesh is used finite element plates
- Topological optimization
The option allows to carry out a design calculation to determine the optimal distribution of the material to improve the mass-stiffness characteristics of the product
- all the time increases the complexity of modern technical solutions;
- there is a need for optimizing the design for weight and size and other parameters to improve the competitiveness of the product;
- the design is carried out in the shortest possible time;
- often there is no possibility of costly full-scale testing of products.
The purpose of the appearance of the built-in analysis of strength
To enable the designer at the early stages of the design to make the right and informed design decisions using the built 3D-model. This undoubtedly improves the quality and saves time spent on product development, and thus making it competitive!
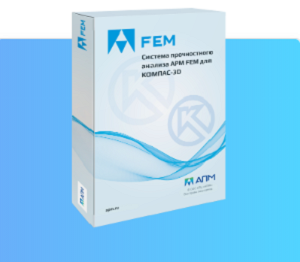
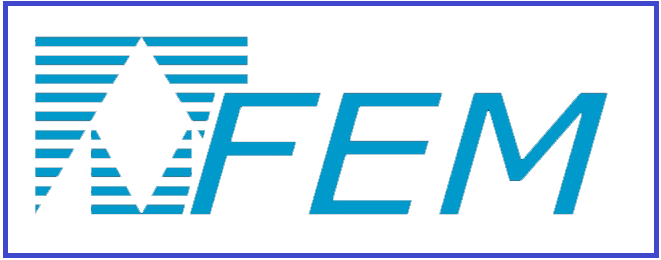
- Set the boundary conditions (fixing and external loads).
- Automatically generate a finite element mesh on a 3D model (with both constant and variable partitioning steps required for models with complex geometric transitions).
- Select the desired type of calculation and perform it.
- Visualize different types of results for further analysis and preparation of a text report.
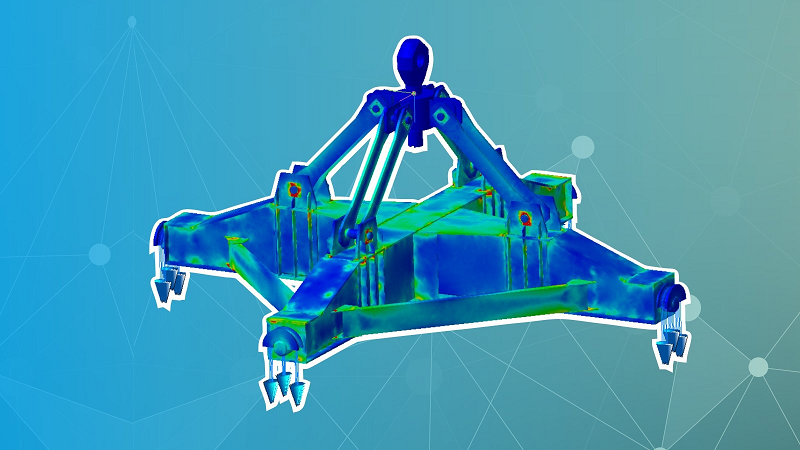
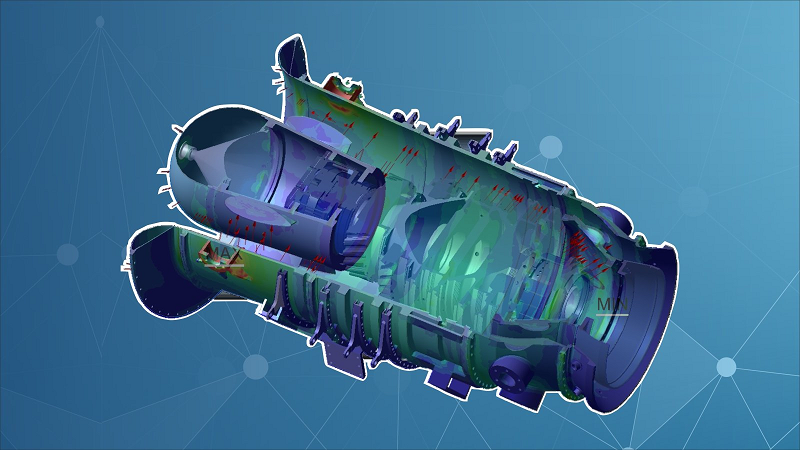
- Static calculation.
- Calculation of sustainability.
- Calculation of natural frequencies (resonance) and vibration modes.
- Topological optimization.
- Calculation of the stationary heat conduction problem.
- The calculation of the problem of thermoelasticity (with the joint implementation of static and thermal calculations).
- Single core and interface KOMPAS-3D.
- The KOMPAS-3D interface provides the user with simplicity and ease of operation for both the geometric and the calculated model.
- The system works directly with the geometric model KOMPAS-3D, without using third-party formats, which reduces the likelihood of errors.
- Integration with full-featured CAE APM WinMachine system .
- Technical support and qualified assistance on all issues from the Russian developer company.
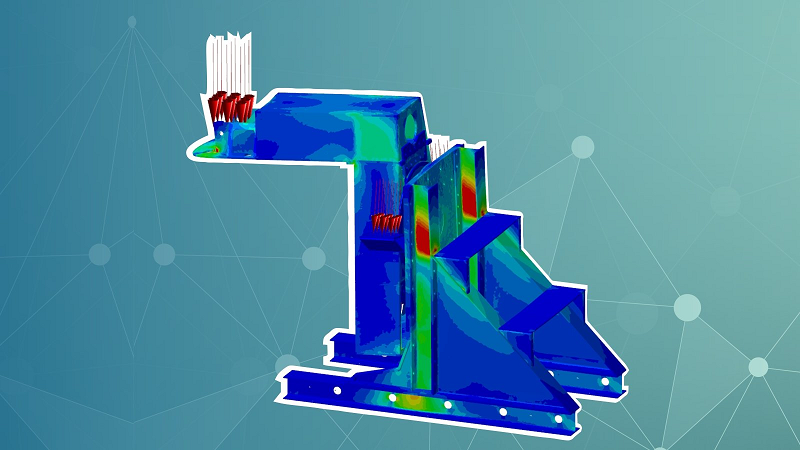
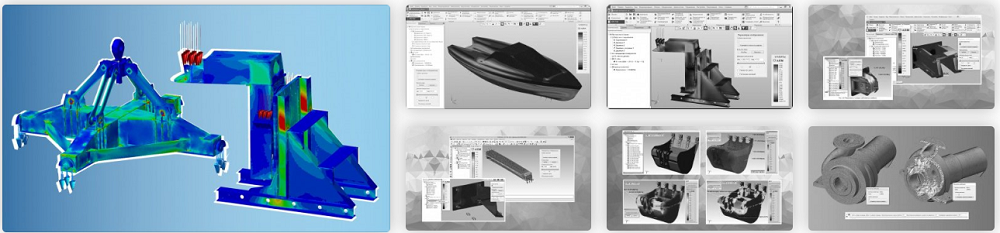
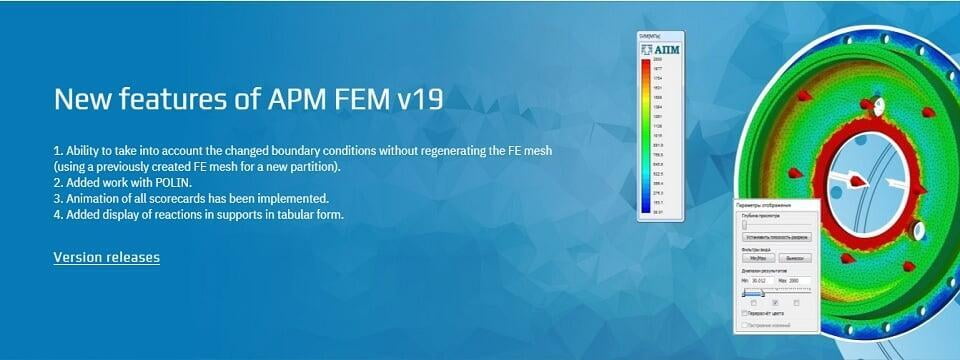
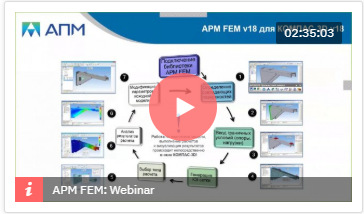
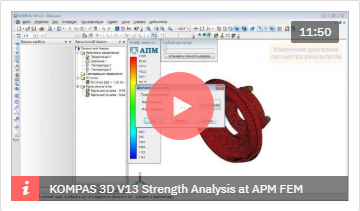