APM TOPOLOGY OPTIMIZATION
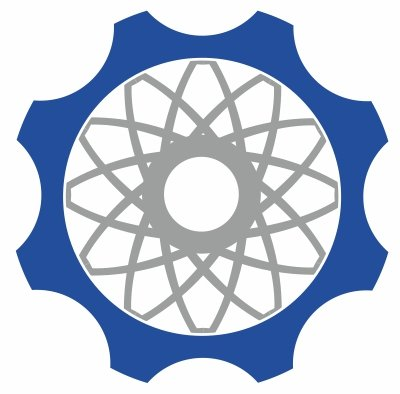
Topological optimization of structures
Modern approach to design involves the effective use of materials in the design. Weight reduction allows you to achieve better energy efficiency and environmental performance of products, reduce their transport and operating costs.
Topological Optimization (MOT) is a computer-aided design method that allows to obtain the optimal shape of the product under the specified operating conditions. The introduction of this tool into the development process allows reducing the time allotted for this stage of the product life cycle, making more extensive use of the possibilities of both traditional manufacturing methods and additive technologies.
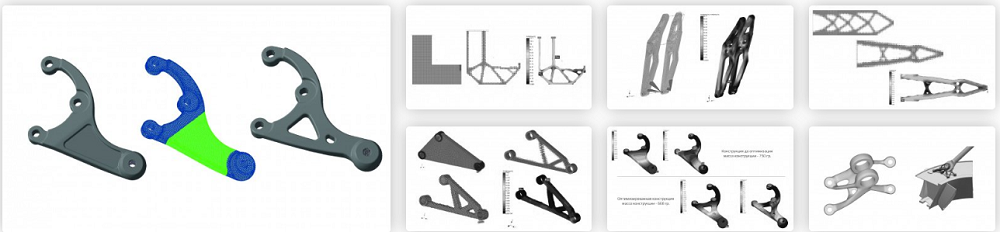
Topological optimization in APM products
Topological optimization became available in the APM software package from the 15th version and its functionality is constantly expanding. The very first was implemented the most popular formulation of the problem of finding the structure of maximum rigidity by the method of "optimal criterion."
From the 16th version, thanks to the introduction of a nonlinear optimizer, it became possible to search for a minimum mass design with allowable stresses, the ability to take into account bulk loads (such as its own weight, acceleration, etc.) and the possibility of applying technological constraints (symmetry, stamping, maximum thickness of part elements). The system has the functionality for the post-processing of maintenance results.

From the 17th version, the user will be able to form an optimization task on his own, setting the objective function and various restrictions that are formed from the following system responses:
- Moving a node;
- Mutual displacement of two nodes;
- Volume / mass of the product;
- Rigidity;
- Voltage in the element;
- Voltage of a group of elements;
- Reaction in the support.
Implemented new technological limitations:
- obtaining self-sustaining structures, extrusion, and some of them have become available for optimization by the method of optimal criteria, which can significantly reduce the number of iterations required to find a solution;
- accounting of volume loads became available for all types of elements and all responses;
- post-processing will be available for the plates.
Topological optimization in the APM environment
The basis for the implementation of topological optimization in the APM environment is the combination of optimization methods and the finite element method. Below are listed the main stages of solving the optimization problem.
The user needs to create a prototype design. For it is necessary to take into account all possible operational loads that can be represented as load cases.
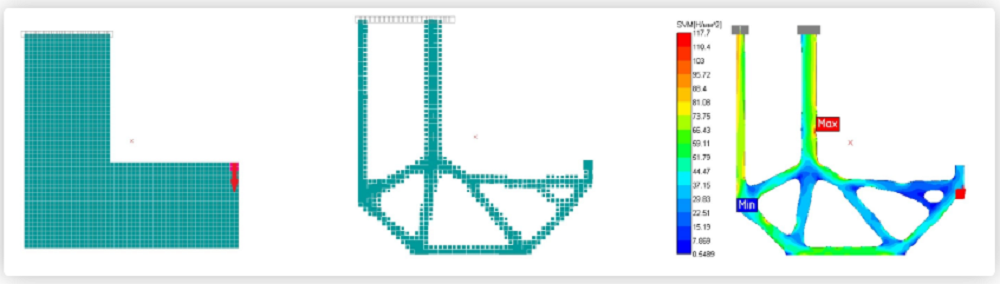
Next, the design space is set, each element of which is assigned a design variable, its value equal to 0 corresponds to the absence of material, and 1 - to complete filling of the material in this final element, this allows you to create an optimization problem, as well as take into account technological limitations.
The last step is the choice of setting the task or its independent formation and launch of the calculation.
After the calculations, post-processing, verification calculation and interpretation of optimization results are performed.
Available functionality
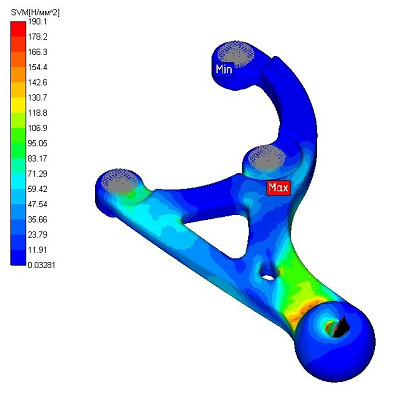
Rigidity maximization is the most popular and fastest method for solving an optimization problem; however, it does not take into account the strength properties of the structure; it is available for all types of finite elements in APM. In the 16th version, it is possible to solve this problem with the help of two algorithms - the “optimal criterion” method and with the help of a more advanced non-linear optimization module. In the second version, accounting for volume forces and technological limitations is available.
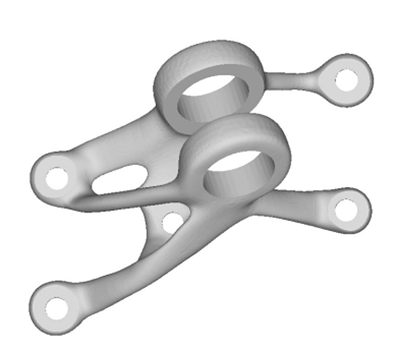
Mass minimization is a popular formulation of the topological optimization problem that allows one to achieve the most lightweight constructions, due to consideration of the strength properties of the material of the part, is available for three-dimensional and two-dimensional finite elements. The algorithm works on the basis of a non-linear optimization module, thanks to which it is also possible to take into account volume forces and technological constraints.
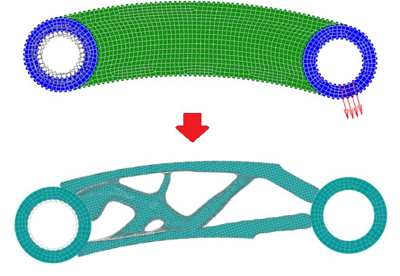
Post-processing is designed to enable verification analysis and further work with the model obtained using topological design optimization. As a result of post-processing on-site design space, a completely new, smoothed surface mesh is created, as well as a voluminous tetrahedral mesh.
APM Structure3D
The core module for finite-element analysis
NEW FEAUTURES
Topology optimization (additional option "TopOpt"). This allows to create the best designs in terms of mass, rigidity and other characteristics.
Topology optimization includes:
- Use multiple load cases / combinations of load cases
- Specify design space
- Manage the sizes of design features
- Several algorithms for processing the final model
- Powerful tools for setting initial parameters
- Analyse calculation results using isosurfaces and color scales, as well as a simplified representation
- Adjust the volume fraction values at arbitrary points in the design area after the calculation
- Post-process optimization results with automatic generation of quality surface mesh with given element size
- Create three-dimensional tetrahedral mesh of optimized design for verification
- Automatically rebuild contact zones taking into account the geometry changes after optimization
- Use GPU (CUDA) to accelerate calculation
- Export optimized model for rapid prototyping via 3D printing or manufacturing with traditional methods (STL format)
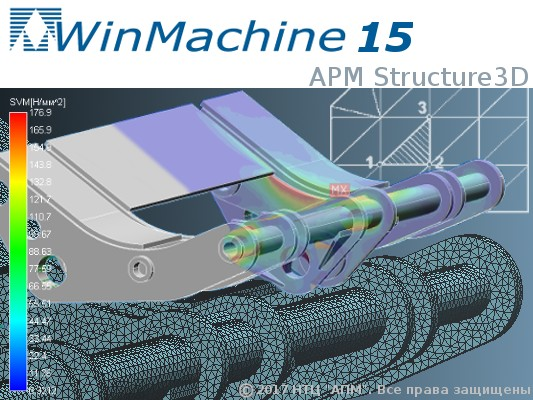
Topological optimization of structures
Designing modern products in a tough competitive environment requires the creation of structures that are optimal in mass, strength, rigidity and other parameters. However, even for an experienced engineer, this is a complex task, the solution of which is not always obvious.
The output can be an automated selection of the optimal design scheme in modern CAD systems using topological optimization!
The company STC "APM" the first in the domestic market of CAD released a software product with the ability to synthesize the optimal design of the product with given parameters and operating conditions.
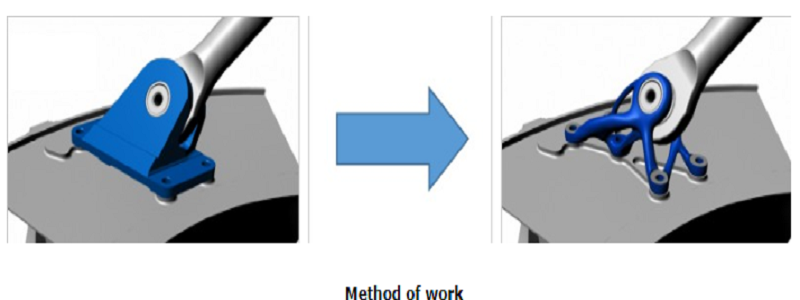
The topological optimization procedure consists of several steps:
Definition of design space - areas where material can be located under the terms of design and technological constraints
Indication of connecting surfaces, effective loads, fixing conditions
The choice of the objective function (depending on the problem to be solved, for example, maximizing the rigidity of the structure)
Limitations are set: mandatory (for example, mass limitation) and technological (for example, the minimum thickness of the elements obtained)
The optimal design is calculated for a given parameter, taking into account the restrictions imposed
The finished design is processed and interpreted by the integrated CAD tools, either exported in STL format to third-party 3D editors or sent to print to a 3D printer.
Result for new products | Result for already manufactured products |
|
|
Attention! To conduct topological optimization of structures, it is necessary to have software from STC “APM” of a version not lower than V16!
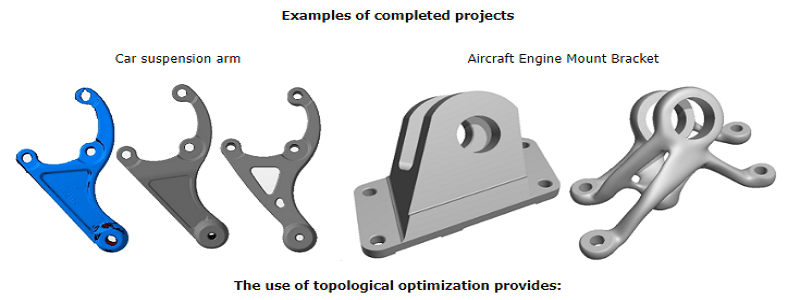
60-70% weight reduction of supporting structures without reducing the strength and rigidity (30-40% without the use of additive technologies);
3-7 times increase in stiffness and strength without increasing mass (2-5 times without using additive technologies);
the change in the lower natural frequencies in times s (effective detuning from the resonance).
Is it possible to perform high-quality reverse engineering and topological optimization using only Russian hardware and software?