UM RCF
UM Rolling Contact Fatigue
UM Rolling Contact Fatigue module is intended for simulation of the accumulation of contact fatigue damages in railway wheels.
The module may be used for implementing of multivariant comparative calculations, for example, for solution of the problem of the wheel tread profile optimization according to a contact fatigue criterion.
UM Rolling Contact Fatigue allows the user
• To define the velocity of accumulation of contact fatigue damages in wheels with the different tread surfaces by using the data which are obtained by simulation of railway vehicle dynamics by means of the UM Loco;
• To consider wheel profile wear-out effect on the rate of accumulation of contact fatigue damages (using module UM Wheel\Rail Wear);
• To represent processes of the stress modeling and the damage accumulation in the wheel with the help of graphic user interface including isolines and coloring.
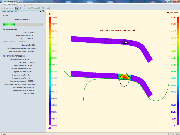
Fatigue strength criterion
The equivalent stress based on the Dang Van’s criterion [1], including amplitude values of the maximum shear stresses and influence of the hydrostatic stress, is used in the module for calculation of contact fatigue strength.The calculated equivalent stresses are compared against to damaging stresses which are defined by means of a wheel steel contact fatigue diagram obtained by using experimental data. The fatigue diagram determines dependency between the number of cycles up to crack/destruction of the wheel material and the equivalent stress level [2, 3].The cumulative damage in a wheel point is defined using the contact fatigue diagram by summation of the calculated damages.
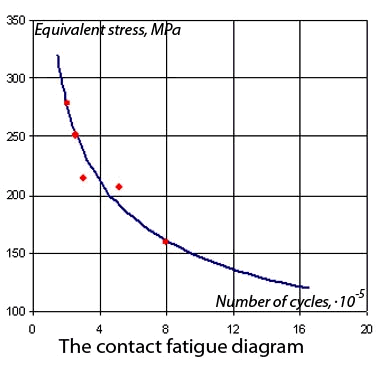
Wheel model
The finite element model of a wheel fragment with the elastic constraints on its surfaces is used [4]. Such a model allows defining the stresses in the subcontact layers of the wheel with the minimum computing time and with the sufficient accuracy. It is convenient to accumulate the contact fatigue damages in the nodes of the finite element scheme also.
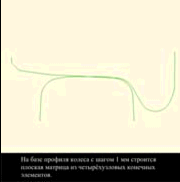
Determination of equivalent stresses
The accumulated fatigue damages correspond to the one radial section of the wheel, which is contacted with a rail once during one revolution of the wheel. So, number of the contact problem solutions is equal to number of the wheel revolutions on the considered running distance.
For solution of the rolling problem in the UM Loco module the model of contact forces of W. Kik and I. Piotrowski and the Kalker CONTACT model are used. With help of these algorithms the normal and tangential forces are calculated at the nodes of the 2D mesh located on the contact surface. As a result of simulation of dynamics of a railway vehicle using UM Loco module the input data file for UM RCF module is created, which contains the values of forces in the contact on each step of the traveled distance.
For increasing speed of calculation of the stresses the FE fragment are separated from the initial FE model of wheel according to contact patch dimension. To the nodes located on all surfaces of the separated fragment except the contact surface the elastic constraints are applied.
In the process of simulation of accumulation of RCF damage in the UM RCF module the obtained forces on each step of the traveled distance are applied to the nodes located on the contact surface of the separated FE fragment of the wheel.
As a result of solution of the problem by FE method the equivalent stresses in the nodes of FE model are determined, which are compared with damaging values according to RCF curve of the wheel steel.
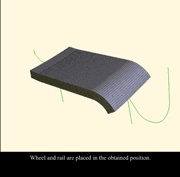

Assumptions
The following assumptions are used.
• The materials of the contacting bodies are uniform, isotropic and elastic.
• The temperature level arising in a wheel does not influence on a stress state and mechanical properties of wheel material considerably.
Example of comparative calculation
The example of calculation of the rate of accumulation of contact fatigue damages in the wheels with the different tread profiles is presented below. Representation by isolines and coloring are used for animated image of the calculation results.
References
1. Ekberg A. Rolling contact fatigue of railway wheels – computer modeling and in-field data / Proceedings of 2nd mini conf. Contact mechanics and wear of rail/wheel systems. Hungary, Budapest. 1996. P. 154…163.
2. Increasing resistance of the railway wheels in operation by using carbonitride hardening of steel / L.M. Shkolnik, D.P. Markov, U.S. Proydak etc. // Herald of the Railway Research Institute (JSC VNIIZhT). 1994. No 6. P. 40…44. (in Russian)
3. Sakalo A.V. Contact fatigue strength of railway wheel steel // Herald of the BSTU. 2011. №2. P. 35…41. (in Russian)
4. Sakalo A.V. Method of simulation of contact stresses by using finite element fragments on elastic foundation // Herald of the VSTU. 2009. №9. P. 71…76. (in Russian)
5. Sakalo A.V. Improvement of the railway wheel tread profile according to a contact fatigue criterion. PhD thesis, Moscow, 2011. (in Russian)
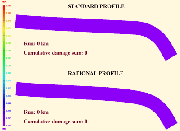
RCF curves are constructed by processing RCF tests results. The test specimens were made from experimental castings of wheel steels having a different chemical composition. Three experimental castings covering the hardness range from 260 to 320 HB were selected for RCF curves constructing.
RCF curves of wheel steel with different hardness are constructed to four RCF criteria.
The obtained RCF curves can be used for modelling of the process of accumulation of the RCF damage for the wheel steels that are close in characteristics to the characteristics of experimental castings.
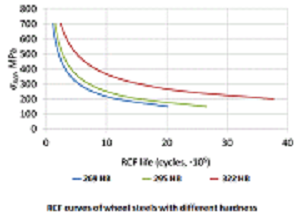
Consideration of wheel profile wear
The wheel wear iteration is a series of calculations within which the profile of the rolling surface of the wheel does not change.
For accumulation of contact fatigue damage in the UM RCF module the FE model of the wheel fragment is used. At the each wheel wear iteration this model is reconstructed. A new FE mesh is constructed on the basis of the worn wheel profile. The damages calculated by means interpolation of the damages accumulated in the nodes of the mesh at the previous wheel wear iteration are assigned to the obtained nodes of the new mesh. Then the procedure of accumulation of RCF damage in the nodes of the new FE mesh of the wheel is repeated.
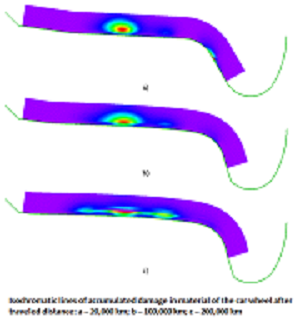
Consideration of residual stresses in wheel material
The residual technological stresses occurring in the process of manufacturing the wheels and the mounting stresses caused by the interference fit of the wheel rim on the wheel plate can be represented as stationary fields in the wheel material. Since the problems of determining such stresses are solved in the axisymmetric formulation, the obtained stress distributions are attributed to one radial section of the wheel.
In process of simulation of the accumulation of RCF damage the field of the alternating loading stresses obtained from the solution of the contact problem is superimposed on the stationary field of the residual stresses, the normal and shear stresses of both fields are summed. Then the value of the criterion of the RCF failure in the nodes of the FE mesh located in the radial section of the wheel is calculated.
The UM library includes two sample files with data of the residual technological stresses in the material of the all-rolled car wheel and the mounting stresses in the material of the locomotive wheel. The files have a simple structure described in UM manual, that allows the user to create and include in the calculation the files with own data.
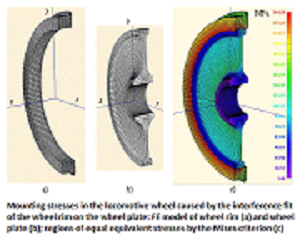
Publications
1. Sakalo V., Sakalo A., Tomashevskiy S., Kerentcev D. Computer modelling of process of accumulation of rolling contact fatigue damage in railway wheels. International Journal of Fatigue 2018;111:7–15.
2. Sakalo A.V. Improvement of the railway wheel tread profile according to a contact fatigue criterion. In: PhD Thesis Moscow State University of Railway Engineering (MIIT), Moscow, 2011 (in Russian).
3. Sakalo A.V. Simulation of accumulation of contact fatigue damages in railway wheel by using finite element fragments on elastic foundation. Vestnik of the Railway Research Institute 2011;4:44–49 (in Russian).
4. Sakalo V.I., Sakalo A.V. Numerical method for solving the contact problems for the solid bodies using the finite element fragments on the elastic foundation. In: Proc. of the 1st joint int. conf. on multibody system dynamics, Lappeenranta; 2010. p. 366–373.
5. Sakalo A.V. Method of simulation of contact stresses by using finite element fragments on elastic foundation. Herald of the VSTU 2009;9:71–76 (in Russian).